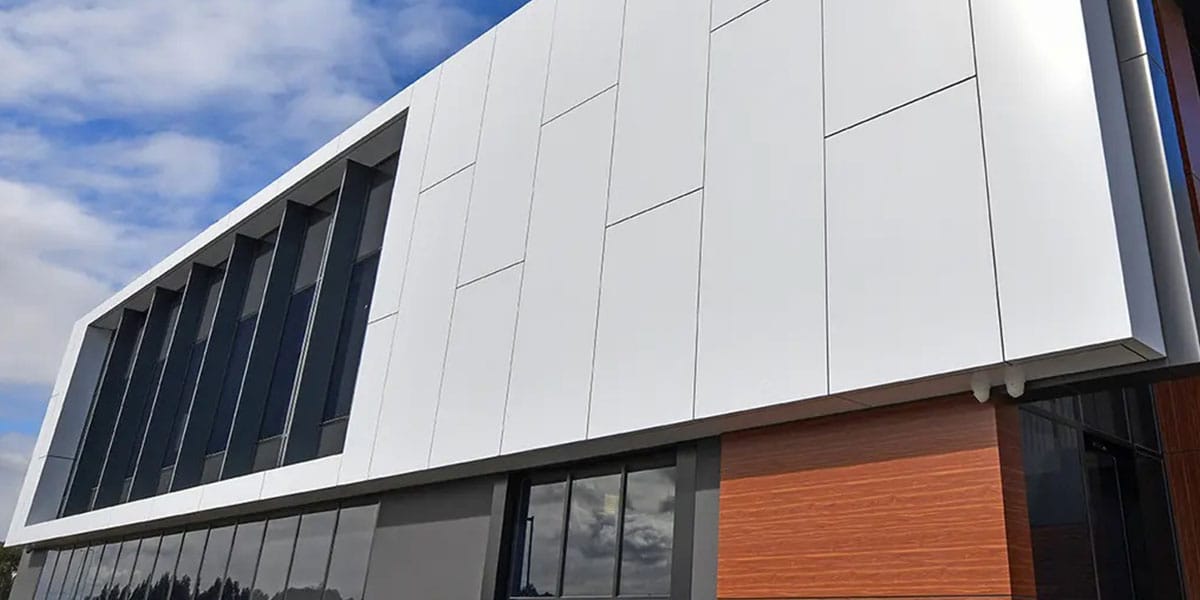
14 Jun A Complete Guide to Aluminum Wall Panels
Table of Contents
Aluminum wall panels serve as protective and decorative surfaces for buildings. These panels appear in both homes and commercial spaces because they handle harsh weather and resist fire. Designers choose aluminum panels for walls due to their ability to form complex shapes and offer a range of colors and finishes. A recent market report shows that aluminum wall panels have gained popularity in construction, with the global aluminum composite panel market valued at $7.19 billion in 2023. Many modern projects use aluminum panels for walls to achieve energy efficiency, safety, and unique designs.
Vitraplate, a prefinished non-combustible aluminum cladding, meets strict fire safety codes and speeds up building approvals, demonstrating both durability and design flexibility.
Key Takeaways
- Aluminum wall panels are strong, lightweight, and resist rust, fire, and harsh weather, making them a durable choice for many buildings.
- There are different types of aluminum panels—solid, composite, honeycomb, and insulated—each offering unique benefits like fire safety, insulation, or strength.
- These panels come in many colors, textures, and shapes, allowing for creative and modern building designs that last long and need little upkeep.
- Installing aluminum panels is faster and easier with proper preparation and tools, and regular cleaning helps keep them looking new for decades.
- Compared to wood, vinyl, and steel, aluminum panels offer better durability, lower maintenance, and greater resistance to weather and fire, providing excellent long-term value.
Aluminum Wall Panels Overview
What Are Aluminum Wall Panels
Aluminum wall panels are building materials made from sheets of aluminium. Manufacturers design these panels to cover and protect both the inside and outside walls of buildings. Aluminum panels for walls come in different shapes and sizes. Most panels have a smooth or textured finish. Some panels look shiny, while others have a matte surface.
Standard sizes for aluminum wall panels depend on the type and use. Many panels measure about 4 feet by 8 feet, but custom sizes are also available. The thickness of each panel can range from 2 millimeters to 6 millimeters. The finish on the surface protects the panel from weather, sunlight, and scratches. Common finishes include powder coating, polyester paint, and PVDF (polyvinylidene fluoride) coating. These finishes help the panels last longer and keep their color.
Note: Studies using advanced imaging show that the core of some panels, like honeycomb types, has a precise structure. The wall thickness and bending radius follow a 10:1 ratio, which helps keep the panels strong and light. Tests also show that smaller honeycomb cells and higher core density improve impact resistance and energy absorption.
Aluminum wall panels have several core features:
- Lightweight but strong
- Resistant to rust and corrosion
- Easy to shape and cut
- Available in many colors and textures
These features make aluminum panels for walls popular in homes, offices, schools, and factories.
Types of Aluminum Panels for Walls
There are several types of aluminum panels for walls. Each type has its own structure and use. The main types include solid, composite, honeycomb, and insulated panels.
Solid Aluminum Panels
Solid panels use a single sheet of aluminium. They are strong and simple. Builders use them for areas that need extra strength or where fire safety is important.
Composite Aluminum Panels
Composite panels have two thin sheets of aluminium with a core material in the middle. The core can be polyethylene or a fire-resistant mineral. These panels are light and easy to install. They also offer good insulation and come in many colors.
Feature | ACM (Aluminum Composite Material) | |
---|---|---|
Core Material | Polyethylene core | Fire-resistant mineral-filled polypropylene core |
Fire Resistance | Lower fire rating (flammable, Class C or lower) | Higher fire rating (Class A or B, fire-retardant core) |
Weight | Lighter (~2.5 lbs/ft²) | Slightly heavier due to denser core |
Cost | Generally less expensive | More costly due to fire-resistant materials |
Applications | Standard construction, budget-conscious projects | High-risk environments requiring strict fire safety |
Honeycomb Aluminum Panels
Honeycomb panels have two sheets of aluminium bonded to a core shaped like a honeycomb. This design makes the panel very strong but still light. The honeycomb core uses alloys like 3003 or 5000 series. The glue used for bonding is safe and does not release harmful gases when burned. Honeycomb panels work well for exterior wall cladding and places that need a high strength-to-weight ratio.
- Honeycomb panels use different coatings for different jobs. PE coating is common for indoor use. PVDF coating is better for outdoor use because it resists weather.
- Tests show that honeycomb panels with smaller cells and higher core density absorb more energy and resist impacts better.
Insulated Aluminum Panels
Insulated panels have a layer of foam or other material between two sheets of aluminium. These panels help keep buildings warm in winter and cool in summer. They also reduce noise from outside.
- Insulated panels are often used in places where energy efficiency is important.
- The thickness and type of insulation can change based on the needs of the building.
Market studies show that aluminum panels for walls come with many coatings, such as polyester, PVDF, and nano-coatings. Each coating offers different benefits, like better UV resistance or easier cleaning. Some panels are made to resist fire, bacteria, or static electricity. These options help builders choose the right panel for each project.
Aluminum wall panels offer a wide range of choices for both design and function. Builders can select panels based on strength, fire safety, insulation, and appearance. The variety of types and finishes makes aluminium panels a flexible solution for many wall applications.
Benefits of Aluminum Panels for Walls
Durability and Longevity
Aluminum panels for walls stand out for their impressive durability. Builders often choose these panels because they resist dents, scratches, and corrosion. The metal does not rust, even in humid or coastal areas. Many commercial-grade wall panels last for decades with minimal signs of wear. This long lifespan makes them a smart investment for both homes and businesses.
Maintenance needs remain low. Owners usually clean the panels with water and mild soap. Unlike wood or vinyl, aluminum does not warp or crack over time. Many manufacturers offer warranties that cover 20 years or more. These features help reduce repair costs and keep buildings looking new.
Weather and Fire Resistance
Aluminum wall panels protect buildings from harsh weather. They shield walls from rain, snow, and strong winds. The panels do not absorb water, so mold and mildew rarely form. In areas with extreme temperatures, aluminum panels expand and contract without losing their shape.
Fire resistance is another key benefit. Noncombustible aluminum panels perform well in fire tests such as ASTM E108. These panels often receive a Class A rating, which means they resist flame spread and penetration. Some commercial-grade wall panels use special coatings with aluminum hydroxide fillers. These coatings form a protective char layer during a fire, slowing heat flow and blocking the spread of gases. Fire endurance tests show that panels with these coatings can maintain steady temperatures for up to 120 minutes, providing valuable time for building occupants to evacuate safely.
Recent building codes now require safer cladding materials. After several high-profile fires, many builders replaced combustible panels with non-combustible aluminum options. This shift helps protect both people and property.
Design and Color Options
Design flexibility sets aluminum panels apart from other materials. Manufacturers offer a wide range of colors, textures, and finishes. Architects can select panels with glossy, matte, or metallic surfaces. Some panels mimic the look of wood, stone, or other natural materials.
Custom shapes and sizes allow for creative building designs. Builders can curve, bend, or cut panels to fit unique spaces. This flexibility makes aluminum panels popular for modern offices, schools, and shopping centers. Homeowners also use them to create bold accent walls or sleek exterior facades.
Tip: Many commercial-grade wall panels come with advanced coatings that resist fading, stains, and graffiti. This feature keeps buildings looking fresh and vibrant for years.
Insulation and Energy Efficiency
Insulated aluminum panels help buildings save energy. These panels use foam or mineral wool cores to block heat transfer. Well-insulated walls keep indoor spaces warm in winter and cool in summer. This reduces the need for heating and air conditioning.
The table below shows how different insulated panel types perform:
Panel Type | Insulation Property | Additional Benefits |
---|---|---|
Polyurethane | High insulating value (high R-value) | Structural strength, suitable for many building types |
Polyisocyanurate (PIR) | Excellent thermal insulation, better fire resistance | Ideal for fire safety priority applications |
Mineral Wool | Good insulation, non-combustible | Superior fire resistance and acoustic insulation |
EPS/XPS | Moderate insulation, cost-effective | Budget-friendly option with decent energy efficiency |
Insulation reduces heat transfer, which lowers energy use for heating and cooling. Buildings with high R-value panels need less energy to stay comfortable. Case studies show that upgrades with insulated aluminum panels can cut energy costs by up to 20%. Owners often see a return on investment within three years. Over time, these savings add up, making insulated panels a smart choice for both homes and businesses.
Aluminum panels also reflect sunlight, which helps reduce heat absorption. This feature lowers cooling costs and supports green building goals. Many commercial-grade wall panels meet strict energy codes and help projects earn sustainability certifications.
Aluminum Wall Panels for Exterior Walls
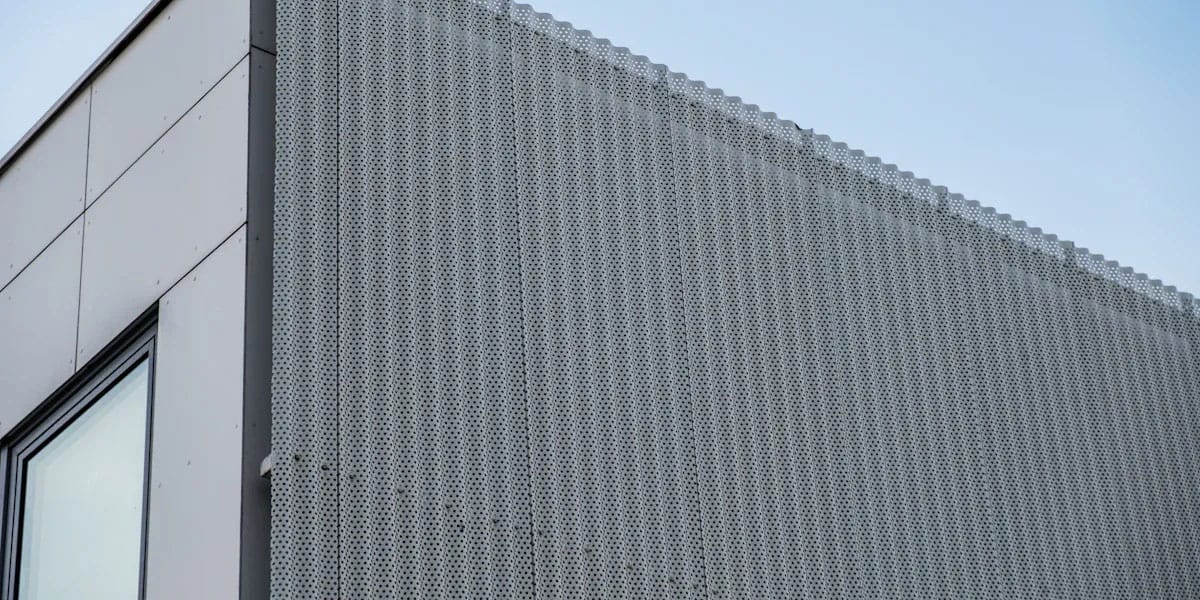
Exterior Applications
Builders use exterior aluminum cladding in many types of projects. These panels protect buildings from rain, wind, and sunlight. Schools, offices, shopping centers, and homes all benefit from aluminum wall cladding systems. Designers often choose exterior aluminum cladding for its modern look and wide range of finishes. Some panels have a smooth surface, while others show off bold textures or colors.
Exterior aluminum cladding works well for both new buildings and renovations. It covers large surfaces quickly and creates a clean, uniform appearance. Many architects use these panels to add visual interest to a building’s facade. In flood-prone areas, exterior aluminum cladding helps prevent water damage and mold growth. The panels also resist pests and rot, making them a smart choice for long-lasting protection.
Tip: Prefabricated exterior aluminum cladding speeds up installation and reduces labor costs. This method also causes less disruption to daily activities around the building.
Performance on Exterior Walls
Aluminum wall panels deliver strong performance on exterior walls. They resist fire, weather, and physical impacts. Many panels earn a Class A fire rating and can withstand up to three hours of fire exposure. This feature helps keep people safe in emergencies. The panels also block water, stopping mold and mildew from forming inside walls.
The table below shows how aluminum wall panels perform in real projects:
Performance Metric | Description / Impact | Case Study Example | Outcome / Benefit |
---|---|---|---|
Fire Ratings | Class A, up to 3-hour fire resistance | Flood-prone residential area | Prevents fire spread, ensures safety |
Durability & Low Maintenance | Resists weather, pests, rot, and impacts | Public library | Low maintenance, long-term savings |
Energy Efficiency | Reduces cooling costs by 20-25% | San Francisco high-rise | 20% lower cooling costs |
Construction Cost Savings | Prefabricated panels lower labor and material costs | New York office building | 15% reduction in construction costs |
Water Resistance | Protects against water damage, mold, and mildew | Flood-prone residential area | Enhanced building protection |
Sustainability | Uses recycled materials, fully recyclable | Eco-friendly office complex | Supports sustainable design |
Installation Efficiency | Quick installation with prefabricated panels | Retail store | Faster project completion |
Aesthetic Versatility | Custom colors, finishes, and textures | Cultural center | Unique design, architectural appeal |
Thermal Insulation | Maintains stable internal temperatures | Texas manufacturing plant | Improved work environment |
Exterior aluminum cladding also stands up to harsh outdoor conditions. The panels use special coatings that slow flame spread and resist corrosion. Aluminum alloys like AA1100H24 and AA3003H24 provide high strength and stability. These panels do not crack under impact. They form a protective oxide layer that stops rust, even in salty or wet climates. Many builders prefer aluminum wall cladding systems for their lightweight design and easy installation.
Note: Dryvit’s Metalite® 3100 and Metalite® 8000 systems show how exterior aluminum cladding can combine strength, beauty, and quick installation. These systems use a rainscreen design to keep moisture out and reduce maintenance needs.
Aluminum Wall Panels vs Other Materials
Steel vs Aluminum Panels
Steel and aluminum panels both serve as strong choices for building walls. Steel panels offer high strength and resist dents well. Many factories and warehouses use steel for its toughness. However, steel weighs more than aluminum. This extra weight can make installation harder and increase shipping costs.
Aluminum panels weigh less and resist rust better than steel. Builders often choose aluminum for projects near the coast or in humid areas. A study by TMS compared the costs of aluminum and steel panels in car manufacturing. The research showed that aluminum panels cost more to make because of higher material and tooling expenses. The study also found that new joining methods, like laser welding and riveting, could lower costs for aluminum in the future. As technology improves, aluminum may become more affordable for large projects.
Wood and Vinyl Alternatives
Wood panels give buildings a classic look. Many people like the natural feel of wood. However, wood needs regular care. It can rot, warp, or attract insects. Vinyl panels cost less and resist moisture, but they can crack in cold weather and fade in the sun.
Aluminum panels last longer than both wood and vinyl. They do not rot or attract pests. Owners spend less time and money on maintenance. Aluminum also works well for decorative wall cladding, offering many colors and textures that mimic wood or stone.
Composite vs Solid Aluminum
Composite aluminum panels have a core material between two thin aluminum sheets. This design makes them light and easy to shape. Solid aluminum panels use a single thick sheet. They offer more strength and fire resistance.
Composite panels suit projects that need flexible shapes and good insulation. Solid panels work best where safety and durability matter most. Builders choose between these types based on the needs of each project.
Choosing Aluminum Panels for Walls
Quality and Customization
Selecting aluminum wall panels involves checking quality standards and customization options. Manufacturers follow strict guidelines to ensure each panel meets industry requirements. The table below shows important quality control statistics and certification details:
Category | Details |
---|---|
Metallic-coated steel face sheets: ASTM A 755/A 755M; Zinc-coated steel: ASTM A 653/A 653M G90; Aluminum-zinc alloy-coated steel: ASTM A 792/A 792M | |
Face Sheet Thickness Options | 0.024 inch (24 gauge), 0.030 inch (22 gauge), 0.036 inch (20 gauge), 0.047 inch (18 gauge) |
Finish System | Fluoropolymer three-coat system: 0.2 mil primer, 0.5 mil polyester base coat, 0.8 mil PVDF top coat |
Manufacturer Qualifications | Minimum 10 years experience; list of 5 similar completed projects with architect and owner details |
Installer Qualifications | Minimum 10 years experience; proof of manufacturer-trained field supervisor |
Field Quality Control | Manufacturer’s field service inspections with written reports; correction of deficiencies |
Warranty | Submission of proposed warranty meeting section requirements |
Customization Options | Color verification samples, multiple surface finishes, ability to match architect’s custom colors |
Compliance | Federal Buy American provisions compliance; independent test reports for substitutions |
Cleaning and Protection | Removal of protective films, cleaning per manufacturer recommendations, replacement of damaged panels |
Manufacturers offer many finishes, colors, and textures. They can match custom colors or create embossed surfaces. These options help architects and owners achieve unique designs while maintaining high quality.
Sustainability Factors
Sustainability plays a key role in choosing aluminum wall panels. Builders and owners look for panels that support environmental goals. The table below highlights important sustainability criteria and studies:
Evidence Aspect | Description |
---|---|
Sustainability Criteria | Economic, environmental, and social factors guide façade system selection, including aluminum panels. |
Life Cycle Assessment (LCA) Tools | ATHENA LCA tool compares environmental impacts of wall systems, focusing on total life cycle. |
Environmental Impact Studies | Studies compare façade materials, showing different impacts based on climate and material type. |
Multi-criteria Decision Methodology | Delphi and Analytic Hierarchy Process (AHP) help rank sustainability in real building case studies. |
Sustainability Ratings Mention | No direct mention of LEED or BREEAM in the reviewed documents. |
Case Study Outcome | Aluminum composite panels evaluated for sustainability in a Sydney building retrofit. |
Many projects use life cycle assessment tools to measure the environmental impact of aluminum wall panels. Builders often choose these panels for their recyclability and long lifespan.
Budget Considerations
Cost remains a major factor when selecting aluminum wall panels. Market reports show that the aluminum curtain wall market could reach USD 49.75 billion in 2025, with a strong growth rate expected through 2035. This growth reflects increased investment and the need for careful budget planning. The Global Wall Panels Market report points out that aluminum panels often have a high initial cost. This can affect project budgets, especially for large buildings. However, many owners find that aluminum panels offer long-term savings because they last longer and need less maintenance. Some companies look for cost-effective wall panel solutions by comparing product types and applications. They also review company profiles and the competitive landscape to find the best value. Careful planning helps owners balance upfront cost with long-term benefits.
Tip: Owners should ask for detailed quotes and compare warranties to make sure they get the best value for their investment.
Installation of Composite Aluminium Panels
Preparation and Methods
The installation of composite aluminium panels starts with careful planning. Workers check the surface it’s being mounted to for flatness and cleanliness. Any dust or debris can affect the bond. They measure the wall and mark the mounting points. This step helps keep the panels straight and even.
Many builders choose easy-to-install wall panels because they save time. They use vhb tape for a strong and quick bond. Vhb stands for “very high bond.” Workers place vhb tape onto the face of the frame. This tape holds the panel in place during mounting. Some projects also use screws or rivets for extra support. The team checks the alignment before pressing the panel onto the frame. They apply steady pressure to make sure the vhb sticks well.
Best Practices
Good installation practices help panels last longer. Workers always follow the manufacturer’s instructions. They use the right tools for cutting and mounting. Sharp blades make clean cuts and prevent damage to the panel edges.
Installers keep the work area dry. Moisture can weaken the vhb bond. They avoid stretching the tape during application. Stretching can reduce the holding power. For best results, they press the panel firmly along the entire edge. This step ensures full contact between the vhb and the panel.
Easy-to-install wall panels make the job faster and safer. Teams inspect each panel after mounting. They look for gaps or loose spots. If they find any problems, they fix them right away. Regular checks during installation help prevent costly repairs later.
Tip: Always store composite panels flat and off the ground before installation. This practice keeps them from bending or warping.
Maintenance and Care
Cleaning Aluminum Wall Panels
Regular cleaning keeps aluminum wall panels looking new. Dust, dirt, and stains can build up on the surface over time. Most owners use a soft cloth or sponge with warm water and mild soap. They gently wipe the surface to remove grime. For tough spots, a soft-bristle brush works well. Avoid using steel wool or harsh chemicals because these can scratch the surface.
Many people rinse the panels with clean water after washing. This step removes any soap left on the surface. Drying the panels with a soft towel helps prevent water spots. For large buildings, a low-pressure hose can clean the surface quickly. Always test any cleaner on a small area first to make sure it does not damage the finish.
Tip: Clean panels at least twice a year. In areas with heavy pollution or near the ocean, clean more often to protect the surface.
Troubleshooting Issues
Sometimes, aluminum wall panels show signs of wear or damage. Common issues include dents, scratches, or fading on the surface. Small scratches often disappear with a gentle polish. For deeper marks, owners may need to use a touch-up kit from the manufacturer.
If a panel becomes loose, check the fasteners and secure them. Water stains on the surface may mean a seal has failed. Replace damaged seals to stop leaks. If the surface shows signs of corrosion, clean the area and apply a protective coating.
The table below lists common problems and solutions:
Problem | Solution |
---|---|
Surface scratches | Use polish or touch-up kit |
Loose panels | Tighten or replace fasteners |
Water stains | Replace seals, clean surface |
Corrosion | Clean and recoat surface |
Note: Always follow the manufacturer’s care instructions for the best results.
Aluminum wall panels offer many advantages for building projects. They provide a strong sign of durability and resist harsh weather. The panels act as a sign of safety because they do not burn easily. Builders see a clear sign of value in their low maintenance needs. The lightweight design is a sign of easy installation and less strain on structures. Owners notice a sign of savings over time because the panels last long and keep their color. The wide range of finishes gives architects a sign of creative freedom. Both homes and businesses use these panels as a sign of modern style and protection.
Cladding Material | Advantages of Aluminum Wall Panels Compared to Other Materials |
---|---|
Wood | Aluminum is more durable, requires less maintenance, and resists weathering, unlike wood which is prone to rot, warping, and pests. |
Vinyl | Aluminum is more resistant to wear, fading, and damage, whereas vinyl cracks and fades over time. |
Stone | Aluminum is lighter, easier to install, and more cost-effective compared to heavy, expensive, and difficult-to-install stone. |
Composite | Aluminum is more cost-effective and longer-lasting than composite materials, which may be more expensive and prone to fading. |
Anyone planning a project should look for the right sign of quality and consult a professional for the best results. Explore the many options in aluminum wall panels to find the perfect sign for your next building.
FAQ
What is the lifespan of aluminum wall panels?
Most aluminum wall panels last 30 years or more. Manufacturers design them to resist rust, fading, and damage. Regular cleaning helps panels stay in good shape for decades.
Can aluminum wall panels be painted or refinished?
Yes, owners can paint or refinish aluminum panels. Many panels come with factory finishes, but repainting is possible. Always use paint made for metal surfaces for best results.
Are aluminum wall panels safe for homes?
Aluminum wall panels meet strict fire safety standards. Builders use them in homes, schools, and offices. These panels do not burn easily and help protect buildings during a fire.
How do aluminum wall panels handle extreme weather?
Aluminum panels resist rain, snow, and strong winds. Special coatings protect them from sun and salt. In coastal or cold areas, these panels keep their shape and color.