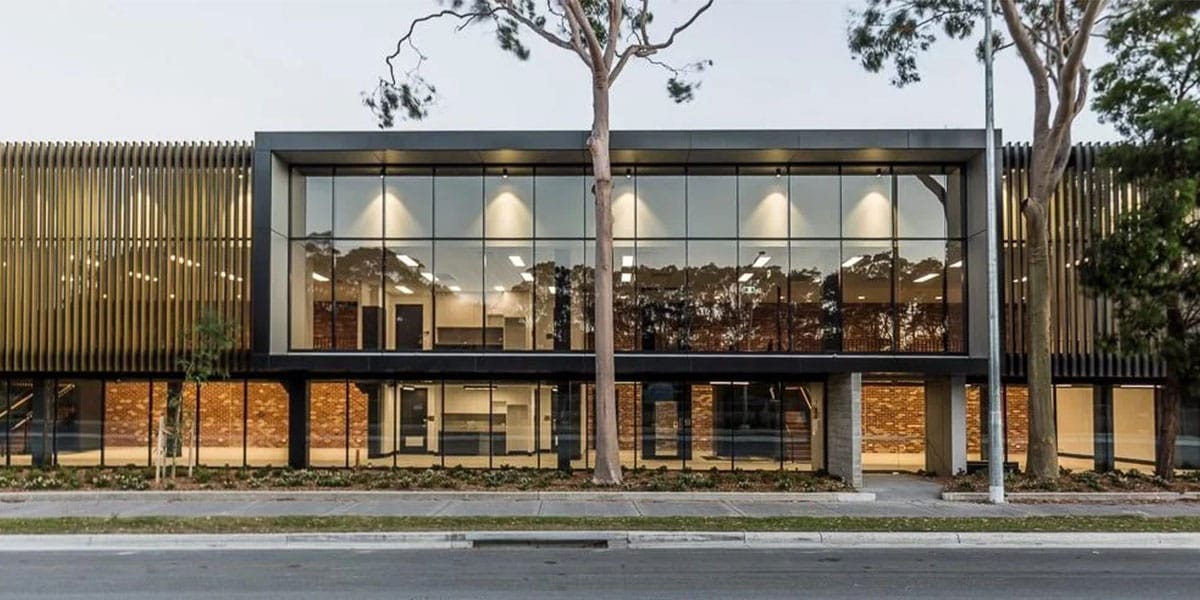
28 Jun What Are the Different Types of Aluminum Composite Panels and Their Features
Table of Contents
Several different types of aluminum composite panels exist, each offering unique features and uses for construction and design projects. The market for aluminium composite panels shows strong growth, with a global size reaching USD 7.5 billion in 2024 and projected to rise to USD 12.6 billion by 2034.
Metric | Value/Description |
---|---|
Global Market Size (2024) | USD 7.5 billion |
Projected Market Size (2034) | USD 12.6 billion |
CAGR (2025-2034) | 5.4% |
Leading Application | Building and Construction |
These panels stand out due to properties like fire resistance, durability, low maintenance, and a variety of finishes. Different types of aluminum composite panels serve specific needs, from high-rise cladding to interior decoration. Choosing the right aluminium composite panel depends on the project’s safety, design, and performance requirements.
Key Takeaways
- Aluminum composite panels combine lightweight design with strong durability, making them easy to install and ideal for many building projects.
- Different types of panels, like ordinary, fire-rated, mirrored, honeycomb, and metal composite, offer unique features to meet specific safety, design, and strength needs.
- Fire-rated panels provide extra safety by limiting fire spread, making them essential for high-rise buildings, hospitals, and schools.
- Panels come in many colors and finishes, allowing creative and modern designs for both interior and exterior uses.
- Choosing the right panel involves balancing durability, fire safety, cost, appearance, and environmental impact to fit your project’s needs.
What Are Aluminium Composite Panels
Structure & Core Materials
Aluminium composite panels, often called acp sheet, have a unique layered structure. Each acp sheet consists of two thin aluminum sheets bonded to a non-aluminum core. The most common core material is a blend of low-density and high-density polyethylene. Some acp sheet types use fire-retardant cores, which include minerals like alumina trihydrate or magnesium hydroxide for added safety. This structure makes aluminium composite panels much lighter than solid metal sheets, yet they remain strong and rigid.
Aspect | Details |
---|---|
Core Composition | |
Panel Construction | Two aluminum facers bonded to the core |
Weight | About half the weight of solid aluminum panels |
Rigidity | Ten times more rigid than solid aluminum of equal thickness |
Weather Resistance | UV stable, moisture resistant, tolerates temperature changes |
Environmental Impact | 100% recyclable core and aluminum facers |
The acp sheet can be easily cut, folded, or shaped using standard tools. This flexibility allows architects to use aluminium composite panels in many creative ways. The core material also provides insulation, helping to keep buildings comfortable and energy efficient.
Key Characteristics
Aluminium composite panels stand out due to several key characteristics. The acp sheet offers a high strength-to-weight ratio, making it easy to handle and install. The aluminum outer layers give the acp sheet excellent durability and resistance to corrosion. The core material adds insulation and helps absorb sound, making the acp sheet useful for both exterior and interior applications.
Note: ACP sheet panels can reduce energy use by up to 20% due to their insulation properties.
The key characteristics of aluminium composite panels include:
- Lightweight design for easy installation
- High rigidity and flatness for a smooth appearance
- Strong bond strength between layers for long-term durability
- Weather resistance, including UV and moisture protection
- Fire resistance in specialized acp sheet types
- Wide range of finishes and colors for design flexibility
Characteristic | Measurable Value / Description |
---|---|
Aluminum Skin Thickness | |
Bond Strength | Minimum 22.5 inch-pounds/inch |
Impact Resistance | Resists small missile impacts (ASTM E1996) |
Thermal Expansion | 1/8 inch over 8 feet per 100°F change |
Panel Flatness | Controlled cooling prevents bowing and twisting |
The acp sheet also meets strict industry standards for safety and performance. As a construction material, aluminium composite panels have become popular in modern architecture. The building and construction sector uses the most acp sheet, especially in regions like Asia-Pacific, where urbanization is rapid. The aluminium composite material provides insulation, durability, and a modern look, making it a top choice for architects and builders.
Different Types of Aluminum Composite Panels
Aluminum composite panels come in several varieties. Each type has a unique structure, core material, and set of features. The different types of aluminum composite panels serve specific needs in construction, design, and safety.
Ordinary ACP Sheets
Ordinary acp sheet panels use two thin aluminum layers bonded to a polyethylene core. This structure creates a lightweight panel with good strength and flexibility. The surface of the acp sheet often features a protective coating, such as PVDF or polyester paint, which adds weather resistance and color variety. These panels work well for both indoor and outdoor applications, including cladding, partitions, and signage.
Ordinary acp sheet panels offer a strong strength-to-weight ratio, easy installation, and resistance to weather and impact. Their lightweight nature reduces structural load and makes them suitable for high-rise buildings.
Feature/Property | Description |
---|---|
Structure | Two aluminum alloy sheets with a non-toxic polyethylene core |
Protective Coatings | PVDF for outdoor use; polyester for indoor use |
Weight | 3.5–5.5 kg/m² |
Basic flame retardant properties | |
Maintenance | Easy to clean and pollution resistant |
Processability | Can be cut, bent, drilled, and shaped easily |
The core and surface materials differ among the different types of aluminum composite panels. Ordinary acp sheet panels use a standard polyethylene core, while other types may use mineral-filled or fire-retardant cores for added safety.
Fire-Rated ACP Sheets
Fire-rated acp sheet panels use a special core made from mineral materials, such as alumina trihydrate or magnesium hydroxide. This core limits flame spread and reduces heat release during a fire. The aluminum layers and fire-resistant coatings further improve safety.
Scientific studies show that fire-rated acp sheet panels control fire propagation much better than standard panels. In large-scale fire tests, fire-rated panels kept flame heights under 10 feet and peak heat release rates below 1 MW. Standard acp sheet panels, by comparison, allowed flames to reach over 25 feet and heat release rates above 6 MW. The fire-resistant core and charring insulation layers make these panels a safer choice for buildings that require strict fire safety standards.
Fire-rated acp sheet panels meet international fire safety codes and are often required in high-rise buildings, hospitals, and schools.
Mirrored ACP Sheets
Mirrored acp sheet panels have a reflective surface finish that mimics the look of glass or polished metal. The core structure remains similar to ordinary acp sheet panels, but the outer aluminum layer receives a special mirror coating. This finish creates a striking visual effect and adds depth to architectural designs.
Mirrored acp sheet panels are lightweight and easy to install. They resist corrosion and maintain their shine over time. Designers often use these panels for interior decoration, signage, and building facades where a modern, reflective look is desired.
Honeycomb Panels
Honeycomb panels use a unique core made from aluminum arranged in a honeycomb pattern. This design reduces weight by up to 30% compared to solid panels, while increasing stiffness and strength. The honeycomb core absorbs energy and resists bending, making these panels ideal for demanding structural applications.
- Research shows that honeycomb panels maintain high stiffness and strength after repeated load cycles.
- The honeycomb core mass should be about 50–66.7% of the total panel mass for optimal performance.
- Honeycomb panels offer better energy absorption and bending stiffness than many commercial products.
The lightweight nature of honeycomb panels makes them suitable for large surfaces, ceilings, and furniture. Their structure also provides excellent sound and thermal insulation.
Metal Composite Panels
Metal composite panels, often called MCM panels, use two thick metal skins bonded to a plastic or fire-retardant core. While aluminum is the most common metal, some panels use steel or copper for added strength or visual appeal. The composite structure gives these panels superior mechanical properties compared to solid metal sheets.
Property | Non-laminated Wood-based Composite | Metal Composite Panels (Aluminum-laminated) |
---|---|---|
Dimensional Stability | Lower | Higher |
Modulus of Elasticity (Eapp) | Baseline | |
Modulus of Rupture (MOR) | Baseline | Increased by 570% (MDF laminate) |
Shear Edgewise Strength | Baseline | Increased by up to 77% |
Metal composite panels offer high dimensional stability, increased modulus of elasticity, and improved rupture strength. The use of thick metal skins and advanced bonding techniques results in panels that resist swelling, expansion, and mechanical stress. These panels are often chosen for projects that require extra durability, impact resistance, or unique metal finishes.
Metal composite panels stand out among the different types of aluminum composite panels for their strength, versatility, and ability to meet demanding architectural requirements.
Material and Manufacturing Differences
The different types of aluminum composite panels use a variety of core and surface materials to meet specific needs. Some panels use low-density polyethylene, while others use mineral-filled or fire-retardant cores. The aluminum skins may receive coatings such as PVDF, FEVE, or polyester paint, and can be finished in many colors and patterns. These differences in material composition affect fire resistance, durability, and appearance.
Importance and Impact | |
---|---|
Technological Advancements | Improved fire resistance, insulation, durability, weather resistance, UV protection, and anti-scratch features. |
Nanotechnology Integration | Enables self-cleaning, anti-bacterial, and anti-pollution properties. |
Automation and Digitization | Enhance production efficiency, reduce waste, lower costs, and increase accessibility of ACPs. |
Eco-friendly Production Methods | Use non-toxic adhesives and recyclable materials for sustainability. |
Customization Technologies | 3D and digital printing allow bespoke designs for architects and designers. |
Regulatory Compliance | Critical for meeting stringent fire safety standards, requiring R&D investment and advanced materials. |
Raw Material Sourcing & Supply Chain | Affect production costs and market competitiveness. |
These manufacturing differences play a key role in the quality, safety, and versatility of the different types of aluminum composite panels. Advanced production methods allow for better fire resistance, improved finishes, and more sustainable products.
Features & Uses
Strength & Durability
Aluminum composite panels show excellent durability in many environments. The acp sheet combines aluminum skins with a strong core, creating a lightweight yet strong material. This structure gives the acp sheet a high strength-to-weight ratio, making it ideal for construction projects that need both stability and easy handling. The panels resist scratches, ultraviolet light, and high corrosion resistance, which helps them last longer on building exteriors. ASTM International standards confirm the durability and performance of these panels. Many acp sheet types maintain flatness and resist bending, even after years of use. The durability of the acp sheet supports its use in demanding applications like cladding and façade cladding.
Fire Resistance
Fire-rated acp sheet panels use mineral-filled cores to improve fire resistance. These panels meet strict fire safety codes for buildings such as hospitals and schools. Tests like ASTM E-84 and ASTM E-136 measure flame spread and noncombustibility. Fire-rated acp sheet panels achieve low flame spread indexes and resist ignition, making them suitable for high-rise construction and areas with strict fire regulations. Small-scale fire tests show that these panels slow down combustion and limit fire growth. The fire-resistant core in these acp sheet types adds an extra layer of safety for façade cladding and other critical applications.
Aesthetic Options
The acp sheet offers a variety of colours and finishes, giving architects and designers many choices for creative projects. The panels provide a smooth, flat surface that looks modern and clean. Manufacturers can produce acp sheet panels that mimic wood, stone, or metal, allowing for cost-effective design solutions. The variety of colours and finishes supports versatility in design, making the acp sheet popular for both interior and exterior cladding. The panels accept digital printing and traditional paints, which helps in signage and decorative applications. Their lightweight nature allows easy shaping and bending for unique architectural features.
Tip: The acp sheet’s surface flatness and finish quality make it a top choice for building façade projects that require a modern look.
Common Applications
The acp sheet finds use in many applications across the construction industry. Builders use these panels for cladding on building exteriors, including façade cladding, to improve weather resistance and appearance. The acp sheet also appears in interior wall panels, ceilings, and partitions. Its lightweight property makes installation quick and reduces structural load. The panels provide thermal and acoustic insulation, which helps keep buildings comfortable and energy efficient. Other common applications include signage, furniture, and transportation. Case studies show that acp sheet panels meet international standards for quality and safety. Their versatile application and excellent durability make them a trusted choice for projects around the world.
Application Area | ACP Sheet Benefit |
---|---|
Building Facade | Lightweight, durable, weather resistant |
Interior Cladding | Easy to shape, variety of finishes |
Signage | Smooth surface, printable, cost-effective |
Furniture | Modern look, easy fabrication |
Transportation | Lightweight yet strong, corrosion resistant |
Comparison & Selection
Summary Table
A summary table helps compare the main types of aluminum composite panels. This table shows how each type performs in key areas like strength, fire resistance, and common cladding applications. By organizing the data, readers can see which panel fits their needs best.
Panel Type | Strength & Durability | Fire Resistance | Aesthetic Options | Common Applications | Sustainability Features |
---|---|---|---|---|---|
Ordinary ACP | High | Basic | Many finishes | Cladding, signage, interiors | 100% recyclable core and skins |
Fire-Rated ACP | High | Excellent | Many finishes | High-rise cladding, hospitals, schools | Mineral core, recyclable |
Mirrored ACP | Moderate | Basic | Reflective look | Interior cladding, signage | Recyclable aluminum |
Honeycomb Panel | Very High | Good | Limited | Large cladding surfaces, ceilings | Lightweight, recyclable |
Metal Composite | Very High | Good | Metal finishes | Demanding cladding, facades | Durable, recyclable |
Note: Summary tables combine different performance metrics, making it easier to compare panel types for cladding and other applications.
Choosing the Right Panel
Selecting the best aluminum composite panel for cladding or other applications involves several steps:
Check the panel’s durability and resistance to weather for long-lasting cladding.
Consider fire safety. Fire-rated panels work best for high-rise or public buildings.
Compare installation costs, including labor and materials, to find a cost-effective solution.
Look at the panel’s lifetime value. Panels with low maintenance and long life offer better value.
Balance your budget with your project’s needs for strength and appearance.
Think about sustainability. Choose panels that are 100% recyclable and meet environmentally responsible criteria.
Review case studies of similar applications to see which panels performed best.
The aluminum composite panel market continues to grow as more builders seek panels that balance performance, cost, and sustainability. Panels with a 4mm thickness and PVDF coating hold the largest market share because they offer a strong mix of durability and weather resistance. Fire-retardant panels lead in safety for cladding in construction. By following these steps, project teams can select panels that meet both technical and environmentally responsible criteria.
Aluminum composite panels differ in core materials, finishes, fire resistance, and strength. Knowing these differences helps builders and designers choose the best panel for each project.
- The bending stiffness of panels links directly to material properties, guiding choices for strength.
- Dent resistance depends on dynamic yield strength and thickness.
- Aluminum alloys show unique formability, so understanding their behavior reduces defects and improves quality.
- Early collaboration with suppliers lowers manufacturing issues and helps select the right alloy.
Recent research uses expert interviews and market data to give reliable insights. These methods help stakeholders understand trends, challenges, and opportunities, making it easier to select the right panel for any application.
FAQ
What is the main advantage of aluminum composite panels?
Aluminum composite panels offer a high strength-to-weight ratio. They remain lightweight yet strong. Builders find them easy to install. These panels also resist weather and corrosion.
Are fire-rated ACP sheets required for all buildings?
Fire-rated ACP sheets are not required for every building. High-rise buildings, hospitals, and schools often need them. Local building codes set the rules. Always check regulations before choosing a panel.
Can aluminum composite panels be recycled?
Yes, aluminum composite panels are recyclable. Manufacturers use recyclable aluminum skins and core materials. Recycling helps reduce waste and supports sustainable building practices.
What finishes are available for ACP sheets?
ACP sheets come in many finishes. Options include solid colors, metallic, wood grain, stone, and mirror. Designers can choose finishes to match any project style.
How do honeycomb panels differ from ordinary ACP sheets?
Honeycomb panels use a core with a honeycomb pattern. This design increases stiffness and reduces weight. Ordinary ACP sheets have a solid polyethylene or mineral core.