
04 Jul Aluminum Wall Panel Options Compared for Modern Construction
Table of Contents
- 1 Key Takeaways
- 2 Aluminum Wall Panels Overview
- 3 Cost Comparison
- 4 Durability and Performance
- 5 Aesthetics and Design
- 6 Installation Methods
- 7 Aluminum Composite Panels
- 8 Solid Aluminum Panels
- 9 Aluminum Corrugated Panels
- 10 Aluminum Perforated Panels
- 11 Aluminum Honeycomb Panels
- 12 Insulated Metal Wall Panel
- 13 Aluminum Exterior Wall Panels
- 14 Best Wall Panels for Different Needs
- 15 Metal Wall Panel vs. Other Materials
- 16 Comparison Table
- 17 FAQ
Multiple types of aluminum wall panels now shape modern construction, offering unique advantages for both home and commercial building projects. The global metal wall panel market reached $7.5 billion in 2023, with aluminum panels favored for their lightweight strength and flexible design. These exterior wall panels deliver durability and energy efficiency, meeting the needs of residential and commercial building owners alike. Growing demand for exterior wall panels and insulated metal wall panel systems reflects a shift toward sustainable, high-performance solutions.
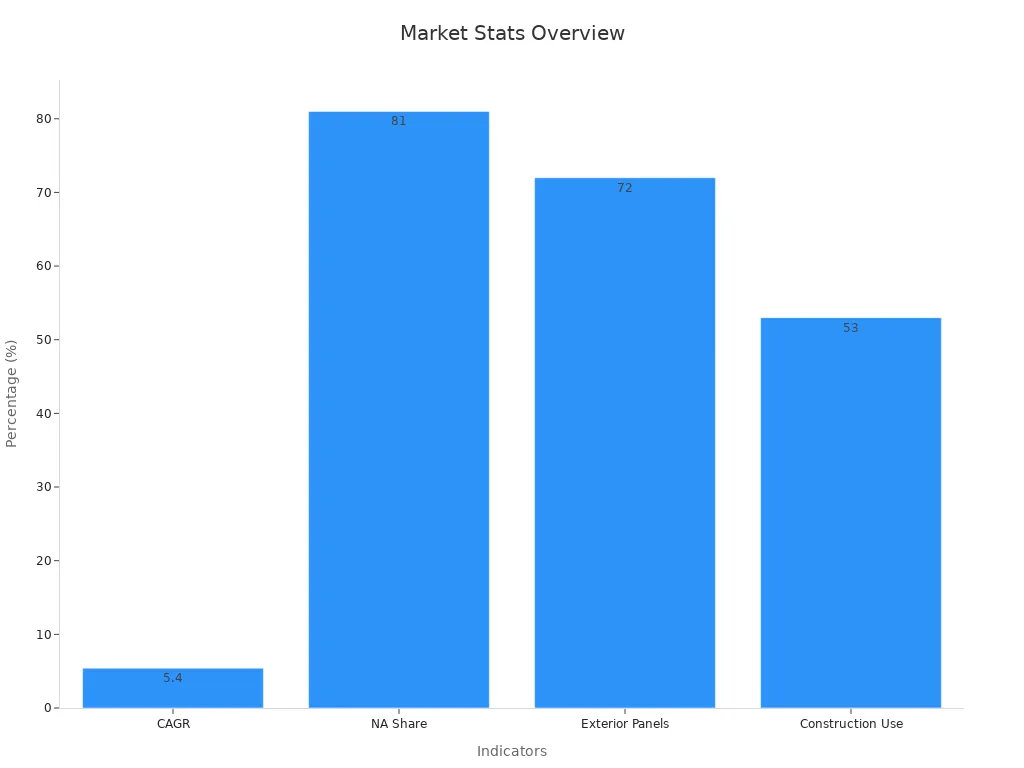
Selecting the right exterior wall panels depends on project goals, budget, and design vision. Each option brings distinct features to consider for any home or commercial building.
Key Takeaways
- Aluminum wall panels come in various types like composite, solid, corrugated, perforated, honeycomb, and insulated panels, each offering unique benefits for different building needs.
- These panels provide strong durability, weather resistance, and energy efficiency, making them ideal for both residential and commercial construction projects.
- Choosing the right panel depends on factors like budget, design goals, installation complexity, and long-term value, including maintenance and energy savings.
- Aluminum panels offer flexible design options with many finishes and customization choices, allowing buildings to achieve modern, attractive appearances.
- Proper installation and insulation improve panel performance, while regular inspections and simple cleaning help maintain their durability and appearance for decades.
Aluminum Wall Panels Overview
Types
Aluminum wall panels come in several forms, each designed for specific construction needs. The North America Metal Wall Panels Market Report 2025 highlights a broad classification of these panels by material, application, and installation method. The most common types include:
- Aluminum Composite Panels (ACP): These panels feature a core material, often polyethylene or fire-rated mineral, sandwiched between two aluminum sheets. ACPs are popular for their lightweight structure and design flexibility.
- Solid Aluminum Panels: Made from a single sheet of aluminum, these panels offer high strength and durability. They are often used in high-traffic or demanding environments.
- Aluminum Corrugated Panels: These panels have a wavy profile, providing extra rigidity and a distinctive appearance. They suit both industrial and modern architectural styles.
- Aluminum Perforated Panels: With custom patterns of holes or slots, these panels allow for ventilation, light diffusion, and unique visual effects.
- Aluminum Honeycomb Panels: These panels use a honeycomb core for exceptional strength-to-weight ratio, making them ideal for large facades and curtain walls.
The Aluminum Cladding Panel Market Report 2034 further segments aluminum cladding by fire rating, surface treatment, and installation method. Applications include wall cladding, roofing, facades, and interior paneling. North America leads the market, driven by urban growth and advanced construction practices.
Key Features
Aluminum wall panels deliver a range of performance benefits that make them a top choice among the types of metal wall panels. Key features include:
Aluminum cladding systems must meet strict building codes, including wind load resistance, thermal movement accommodation, and positive drainage design.
Feature | Performance Benchmark / Standard |
---|---|
Insulation | Closed-cell Polyisocyanurate with glass fiber reinforced foil facers |
Density | 2.0 pcf (ASTM D1622) |
Compressive Strength | 25 psi (ASTM D1621) |
Flame Spread | 25 or less (ASTM E84) |
Water Vapor Transmission | Less than 0.3 perms (ASTM E96) |
Dimensional Stability | Less than 2% linear change (ASTM D2126) |
Warranty | 2 years on materials/workmanship, 20 years on finish, 10 years panel integrity |
Manufacturers use advanced technologies such as cold spray particle deposition for seam sealing and friction stir welding for enhanced panel strength. Quality assurance programs and certified installers ensure that aluminum cladding meets high standards for durability and performance. These panels also offer a wide range of finishes, including anodized, coated, and brushed surfaces, allowing architects to achieve both functional and aesthetic goals.
Cost Comparison
Price Factors
Aluminum wall panels present a wide range of cost factors that influence the final price of a construction project. Material type stands out as a primary driver. For example, aluminum composite panels often cost less than solid aluminum or honeycomb panels due to their lightweight core and efficient manufacturing process. Panel thickness also affects the price, with thicker panels providing more strength but increasing material costs.
Custom designs and finishes can raise costs. Panels with intricate perforations or unique textures require specialized production, which adds to the expense. Installation complexity plays a significant role as well. Projects that demand concealed fasteners, curved surfaces, or custom frameworks will see higher labor and support costs.
The following table summarizes the main cost factors and typical price ranges for different aluminum wall panel types:
Panel Type | Cost Range (per m²) | Key Cost Factors | Typical Applications |
---|---|---|---|
Aluminum Composite Panels | $20 – $60 | Lightweight core, versatile, easy installation | Commercial facades, high-rises |
Solid Aluminum Panels | $40 – $80 | Thickness, custom textures, higher material cost | High-impact areas, canopies |
Aluminum Corrugated Panels | $25 – $50 | Profile depth, protective coatings | Industrial buildings, warehouses |
Aluminum Perforated Panels | $30 – $70 | Pattern complexity, panel size | Facades, sunscreens, partitions |
Aluminum Honeycomb Panels | $50 – $120 | Core density, panel size/thickness | High-performance applications |
Other important cost factors include:
- Installation costs, which depend on labor rates and the complexity of the supporting framework.
- Preparation and finishing, such as surface sealing and painting.
- Maintenance requirements, which can vary based on panel type and finish.
- Regional market conditions, with North America and Europe often seeing higher prices due to advanced standards and demand, while Asia-Pacific benefits from competitive manufacturing.
Aluminum panels often reduce installation costs by about 30% compared to steel panels. Their lighter weight means less structural support and easier handling, which lowers labor and shipping expenses. Compared to traditional materials like stone, brick, or wood, aluminum panels offer a cost-effective option for both initial investment and ongoing maintenance.
Value Over Time
When evaluating aluminum wall panels, long-term value becomes a critical consideration. These panels deliver significant savings throughout their lifespan. Their corrosion resistance means less frequent repairs and replacements, especially in harsh climates. This durability supports a strong long-term value proposition for building owners.
Aluminum panels require minimal maintenance. Cleaning and occasional inspections usually suffice, reducing ongoing costs. Their lightweight nature also means less stress on building structures, which can extend the life of the entire wall system.
Long-term value also comes from energy efficiency. Many aluminum wall panels, especially insulated types, help regulate indoor temperatures. This can lower heating and cooling bills, adding to the overall value of the investment.
Case studies show that aluminum panels perform well in demanding environments, maintaining their appearance and function for decades. These panels often outlast alternatives like wood or PVC, which may warp, rot, or fade over time. As a result, the cost comparison between aluminum and other materials often favors aluminum when considering the full lifecycle.
Tip: Building owners should look beyond the initial price and focus on total cost of ownership. Aluminum wall panels often provide the best long-term value due to their durability, low maintenance, and energy-saving features.
Durability and Performance
Weather Resistance
Aluminum wall panels show strong resistance to harsh weather. Manufacturers design these panels to withstand high winds, heavy rain, and flying debris. Wind uplift resistance testing confirms that interlocking panel designs keep water out and protect the building envelope. Durable coatings on the panels help them resist fading and corrosion, even in extreme climates. These coatings also reflect solar heat, which helps keep buildings cooler and improves energy efficiency.
Long-term studies support the reliability of aluminum wall panels. For example, accelerated aging tests simulate years of UV exposure, temperature swings, and moisture. These tests measure changes in color, reflectance, and surface strength. Results show that aluminum panels maintain their appearance and mechanical performance after harsh weathering. A 12-month field study by ORNL tracked panels in real outdoor conditions. The study found that panels with tight air seals performed better in winter, reducing heat loss by up to 54% compared to panels with more air leakage. However, tighter panels can hold more moisture inside the wall cavity during cold months, so proper design is important.
Note: Choosing panels with the right air tightness and moisture control features helps ensure long-term durability in any climate.
Maintenance
Aluminum wall panels require little maintenance over their lifespan. Most panels only need occasional cleaning with water and mild soap to remove dirt or stains. Their smooth surfaces resist mold, mildew, and insect damage, which reduces the need for repairs. Durable finishes protect against scratches and impact, keeping the panels looking new for many years.
Building owners should inspect panels once or twice a year. They should check for loose fasteners, damaged seals, or signs of corrosion around joints. Quick repairs prevent small issues from becoming bigger problems. With proper care, aluminum wall panels can last over 40 years, making them a smart choice for both homes and commercial buildings.
Aesthetics and Design
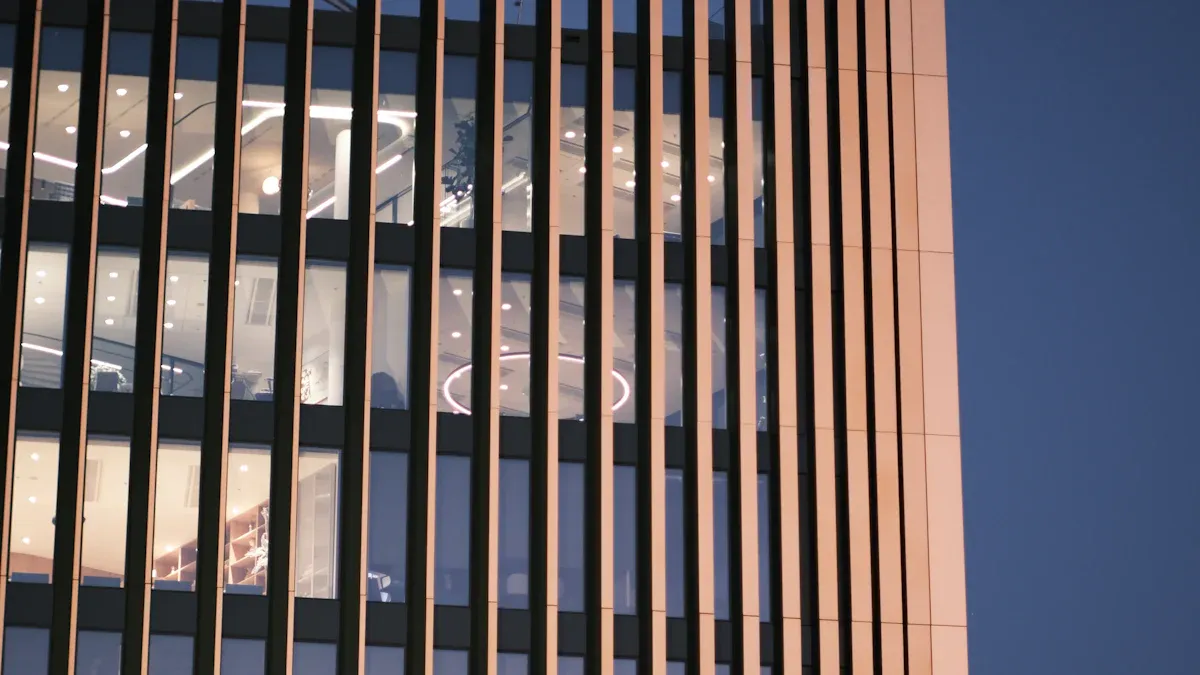
Finishes and Textures
Aluminum wall panels offer a wide range of finishes and textures that appeal to architects and building owners. Manufacturers provide brushed metal finishes in three standard colors and mirror finishes in two standard colors. Many projects use gloss or matte pre-painted aluminum facers, which give designers flexibility to match any style. All these finishes bond securely to a solid polyethylene core, ensuring long-term durability and a consistent look.
Brushed metal finishes (three standard colors)
Mirror finishes (two standard colors)
Gloss and matte pre-painted aluminum facers
These options allow buildings to stand out or blend in, depending on the design vision. Metal cladding panels, including aluminum, remain popular for their attractive appearance and ability to support creative shapes, joinings, and trims. Many consumers choose finishes based on both initial cost and long-term performance. Some experts note that sealant joints can attract dirt and stains, so careful detailing helps maintain a clean look over time.
Tip: Selecting the right finish can help a building resist weathering and keep its appearance for decades.
Customization
Designers and builders value aluminum wall panels for their high level of customization. Custom aluminum panels can be cut to fit around doors, columns, or other architectural features. Some products, like Moxie graphic panels, allow for custom sizes up to 47″x95″ without extra charges. These panels can cover large or small areas and offer several mounting options, such as hidden tape, cleats, decorative standoffs, or cable mounts.
Challenge | Customization Solution | |
---|---|---|
Bioterra Campus, San Diego | Seismic, glass, wind, energy | Deeper profiles, engineered adaptations, fewer drawing revisions |
Northlake Commons, Seattle | Timber anchorage, seismic drift | New dies, dual color finishes, flexible wall systems |
Univ. of Michigan Medicine | Timber anchorage, wind, shading | Early design-assist, solar shading devices, versatile products |
Panels remain lightweight and rigid, making installation easier. Durable finishes, including UV-protected direct prints, resist scratches and impacts for up to 30 years. Many panels achieve a Class A fire rating due to their aluminum layers and bonded core. Real-world projects, such as Monroe Community College and H&R Block, show how custom solutions meet diverse design and performance needs.
Installation Methods
Exposed vs. Concealed Fasteners
Aluminum wall panels can be installed using either exposed or concealed fastener systems. Each method offers unique benefits and trade-offs. Exposed fasteners remain visible on the panel surface. This approach allows for faster installation and requires less skill, making it a popular choice for projects with tight timelines or limited budgets. Many contractors prefer exposed fasteners for industrial buildings or utility structures.
Concealed fasteners, on the other hand, hide all attachment points behind the panels. This method creates a cleaner, more modern appearance. It also protects the fasteners from weather, which can improve the system’s weathertightness and reduce maintenance needs. However, concealed fastener systems take more time to install and often require specialized trim pieces and higher labor costs.
The following table summarizes key differences:
Aspect | Exposed Fasteners | Concealed Fasteners |
---|---|---|
Weathertightness | More potential for water entry, but less concern on vertical walls | Better weathertightness as fasteners are hidden and protected from weather |
Maintenance | Requires yearly inspections to check fasteners and seals | Requires fewer inspections due to protected fasteners |
Easier, faster, less skill required; suitable for DIY | More complex, longer installation; higher costs and more trim needed |
Tip: For high-visibility facades or areas with harsh weather, concealed fasteners often deliver better long-term performance.
Insulation Options
Insulation plays a vital role in the performance of aluminum wall panels. Modern systems, such as the Butlerib II EX and Shadowall EX, use a stanchion design to create a larger insulation cavity. This design allows for more fiberglass insulation, which improves thermal efficiency and helps buildings meet strict energy codes.
These wall systems achieve U-factor ratings as low as 0.046 and 0.047, outperforming many standard insulated metal panels.
Accredited testing, like the BlueScope Guarded Hot Box, confirms real-world energy savings and supports accurate HVAC sizing.
Builders benefit from easier installation, reduced need for heavy equipment, and lower freight costs compared to traditional insulated panels.
Proper insulation not only boosts energy efficiency but also supports occupant comfort and reduces long-term operating costs. Choosing the right insulation option ensures that aluminum wall panels deliver both durability and energy savings for any project.
Aluminum Composite Panels
Description
Aluminum composite panels combine two thin sheets of aluminum with a core made from polyethylene or a fire-resistant mineral. This structure creates a lightweight yet strong material. Manufacturers often refer to this as aluminum composite material. The panels offer flexibility in design, allowing architects to choose from many colors, textures, and finishes. Builders use aluminum composite material for both exterior and interior applications. The panels resist weather, corrosion, and impact, making them suitable for demanding environments. Recent advancements have improved fire resistance and introduced eco-friendly options, supporting sustainability goals in modern construction.
Pros and Cons
Aspect | Pros | Cons |
---|---|---|
Physical Properties | Lightweight, durable, corrosion resistant, easy to fabricate | Combustible core in some panels increases fire risk |
Performance | Good insulation, reduces building load, supports fast installation | Fire safety concerns require careful product selection and compliance |
Economic Factors | Lower shipping and installation costs, long lifespan | Raw material price volatility can affect project budgets |
Regulatory/Safety | Fire-retardant and antimicrobial options available | Some traditional fire tests may not reflect real-world fire behavior |
Note: Fire-resistant aluminum composite material panels dominate the market due to stricter safety regulations. However, panels with polyethylene cores face restrictions in many regions.
Best Uses
- Building exteriors and facades, where lightweight panels reduce structural load and speed up installation.
- Interior finishes, false ceilings, and partitions, offering design flexibility and easy maintenance.
- Signage, displays, and advertising panels, where aluminum composite material provides a smooth surface for printing and engraving.
- Transportation, such as vehicle bodywork and machine casings, benefiting from the material’s durability and weather resistance.
- Sustainable construction projects, where recycled aluminum composite material supports green building certifications.
Aluminum composite panels remain popular in both commercial and residential construction. Their versatility, durability, and attractive appearance make them a preferred choice for architects and builders seeking modern solutions.
Solid Aluminum Panels
Description
Solid aluminum panels consist of a single, thick sheet of aluminum. Manufacturers use advanced techniques to create panels with high strength and consistent quality. These panels do not have a core or layers, which makes them different from composite or honeycomb panels. Solid aluminum panels offer a smooth, flat surface that works well for both exterior and interior walls. Architects often choose these panels for projects that need durability and a clean, modern look.
Technical reviews show that solid aluminum panels perform well under different loading conditions. Studies highlight their strong mechanical properties and reliable structural behavior. Engineers value these panels for their ability to handle wind, impact, and other stresses in building applications.
Pros and Cons
Pros | Cons |
---|---|
High strength and durability | Heavier than composite panels |
Excellent fire resistance | Higher material cost |
Long lifespan | More challenging to fabricate curves |
Low maintenance | Requires strong support structures |
Solid aluminum panels resist corrosion and fire. Their solid structure means fewer worries about delamination or water damage. However, these panels weigh more than other types, which can increase installation effort. The higher cost reflects the quality and performance benefits. Some projects may need extra support to hold the weight of these panels.
Best Uses
- High-traffic areas such as schools, hospitals, and airports
- Building facades that require extra strength and impact resistance
- Canopies, soffits, and entryways exposed to harsh weather
- Projects where fire safety is a top priority
Tip: Solid aluminum panels work best for buildings that need long-term durability and strong protection against the elements.
Aluminum Corrugated Panels
Description
Aluminum corrugated panels feature a wavy or ridged profile that increases their strength and rigidity. Manufacturers form these panels from lightweight aluminum sheets, making them easy to handle and install. The unique shape helps distribute loads evenly, which improves structural performance. Builders often choose aluminum corrugated panels for their durability, weather resistance, and energy efficiency. These panels reflect sunlight, which can help lower cooling costs in warm climates. The market for aluminum corrugated panels continues to grow, driven by urbanization, infrastructure projects, and the demand for sustainable building materials.
- The construction industry values these panels for their corrosion resistance, especially in coastal or humid environments.
- Technological advances have improved panel performance, offering more design options and better durability.
- Customers prefer aluminum corrugated panels for their long lifespan and eco-friendly properties.
Pros and Cons
Aspect | Pros | Cons |
---|---|---|
Weight | Lightweight, reduces structural load | Softer than steel, more prone to denting from hail or debris |
Durability | Corrosion-resistant, ideal for wet or coastal climates | Thicker panels needed for dent resistance, increasing material cost |
Installation | Malleable, allows for diverse profiles and easier installation | Fewer color options and less availability than steel |
Cost | Lower shipping and handling costs | About 35% higher cost than steel roofing due to thicker gauges |
Structural Integrity | Withstands static loads without permanent deformation (ASTM E 1592) | Proper fastening critical, especially in high-wind or hurricane zones |
Note: Engineering tests confirm that aluminum corrugated panels can handle strong winds and heavy loads, but thicker panels may be necessary for areas with frequent hail.
Best Uses
- Schools, offices, and apartment buildings benefit from the durability and modern look of aluminum corrugated panels.
- Fire stations, welcome centers, and industrial facilities use these panels for their weather resistance and low maintenance.
- Builders select aluminum corrugated panels for projects where sustainability and energy efficiency are priorities.
- Design professionals rely on detailed product data and case studies to choose the right panel for each application.
Real-world projects like PIE Center, Nabholz Office Addition, and La Crosse Fire Station #2 show how aluminum corrugated panels perform well in diverse settings, offering both strength and visual appeal.
Aluminum Perforated Panels
Description
Aluminum perforated panels feature a series of holes or slots punched into lightweight aluminum sheets. Manufacturers use computer-controlled machines to create precise and customizable patterns. This process allows architects to select from a variety of shapes, such as circles, squares, or hexagons, to match design needs. The panels often receive advanced coatings or anodizing, which improves corrosion resistance and preserves their appearance over time. These panels stand out for their ability to control light, airflow, and sound, making them a popular choice in modern construction.
Market research shows that demand for aluminum perforated panels continues to rise. Urbanization and new building codes drive the need for energy-efficient and sustainable materials. The panels’ lightweight nature simplifies structural design and reduces installation costs. Projects like the Austin Central Library demonstrate how anodized aluminum perforated panels can provide both durability and visual appeal, even in challenging environments.
Pros and Cons
Pros | Cons |
---|---|
Lightweight and easy to install | May require protective coatings in humid climates |
Customizable patterns for design flexibility | Less structural strength than solid panels |
Excellent ventilation and light control | Can allow water ingress if not properly detailed |
Corrosion-resistant with proper finishes | Higher initial cost for advanced coatings |
Supports energy efficiency and sustainability |
|
Aluminum perforated panels offer a balance of function and style. Their ability to improve airflow and reduce energy use makes them valuable for green building projects.
Best Uses
Aluminum perforated panels serve many roles in construction and industry. Builders often use them for building facades, sunscreens, and decorative cladding. The panels help control sunlight and ventilation, which improves comfort and reduces energy costs. Interior designers use them for partitions, ceilings, and acoustic panels to manage sound and add visual interest.
- Architectural facades: Enhance building exteriors with unique patterns and improved energy performance.
- Interior design: Create partitions, ceilings, and wall features that combine function with aesthetics.
- Industrial and HVAC: Provide ventilation covers and protective screens that resist corrosion.
- Transportation: Reduce weight in automotive and aerospace applications while maintaining strength.
Studies confirm that double-skin facades using aluminum perforated panels can lower heating and cooling needs. The panels’ high strength-to-weight ratio also supports their use in weight-sensitive industries. For best results, manufacturers recommend applying protective coatings in moisture-rich environments to prevent oxidation and extend panel life.
Aluminum Honeycomb Panels
Description
Aluminum honeycomb panels use a core shaped like a honeycomb, sandwiched between two thin aluminum sheets. This design creates a panel that is both lightweight and strong. Engineers often select these panels for projects that need high strength without extra weight. The honeycomb structure gives the panel excellent stability and impact resistance. Many industries, such as aerospace and transportation, use these panels because they perform well under different types of loads. Architects value their ability to reduce noise and vibration in buildings. The panels also provide good heat insulation and can absorb energy during impacts.
- Honeycomb panels show high stiffness and strength compared to solid panels.
- The core design allows for custom shapes and sizes, making them versatile.
- Manufacturers can add features like sound absorption or antenna placement for special uses.
Pros and Cons
Pros | Cons |
---|---|
Lightweight, easy to handle and install | Bonding between core and face sheets can be challenging |
High strength and stiffness for their weight | Directional strength may vary depending on load direction |
Excellent impact resistance and energy absorption | Possible failure modes include delamination and buckling |
Good heat and noise insulation, reduces vibration | Higher cost than standard composite panels |
Recyclable and supports sustainable building practices | Requires precise manufacturing for best performance |
Note: Honeycomb panels outperform wood and foam cores in strength and durability. Their design helps buildings meet strict safety and energy standards.
Best Uses
Aluminum honeycomb panels work well in projects that demand lightweight strength and durability. Architects and builders use them for:
- Building facades and curtain walls that need to resist wind and impact
- Ceilings, partitions, and interior walls where noise reduction is important
- Transportation hubs, airports, and high-traffic public spaces
- Specialized structures like radiation protection buildings or areas needing vibration control
These panels also suit projects focused on sustainability. Their recyclable materials and long lifespan help reduce environmental impact. Optimized honeycomb designs can meet specific needs, such as extra energy absorption or custom shapes for unique architectural features.
Insulated Metal Wall Panel
Description
Insulated metal wall panels combine a metal exterior with a rigid foam core. This design creates a single panel that provides both structure and insulation. Manufacturers use materials like expanded polystyrene, extruded polystyrene, or polyurethane foam for the core. These panels deliver high insulation properties, helping buildings stay warm in winter and cool in summer. The metal skins protect the foam from weather and damage. Insulated metal panel systems often feature tongue-and-groove joints, which reduce air leaks and improve energy efficiency.
Testing organizations such as Factory Mutual and Underwriters Laboratories evaluate these panels for strength, fire safety, and weather resistance. The following table shows common tests and their purposes:
Test Purpose | ASTM Standard(s) | Description |
---|---|---|
Panel strength and structure | ASTM E72-10, ASTM E330/E330M-14 | Measures load resistance and structural integrity. |
Air leakage | ASTM E283, ASTM E1680-11 | Checks how much air passes through the panel system. |
Water penetration | ASTM E331, ASTM E1646-95 | Assesses resistance to water under pressure. |
Fire performance | NFPA 285, IBC Chapter 26 | Evaluates fire safety for assemblies with foam insulation. |
Pros and Cons
Insulated metal wall panels offer many advantages. They provide continuous insulation, which reduces heating and cooling costs. The panels resist mold, moisture, and pests. Builders can install them quickly, saving time and labor. The panels also meet strict fire and weather safety codes.
However, some foam cores contain chemicals that raise environmental concerns. Polyurethane foam, for example, offers the highest R-value per inch but costs more and may have limited thickness options. Panels must be sealed well to prevent moisture problems.
Core Type | R-value/inch | Strength (psi) | Pros | Cons |
---|---|---|---|---|
EPS | 3.6 | 10 | Affordable, easy to modify | Lower strength, possible flame retardant issues |
XPS | 5.0 | 20 | Strong, water resistant | Availability issues, chemical concerns |
PUR | 6.54 | 35 | Highest insulation, strong | Most expensive, limited thickness |
Tip: Proper sealing and weather barriers help prevent moisture issues and extend panel life.
Best Uses
Insulated metal wall panels work well in many building types. Commercial, industrial, and educational facilities use these panels for their energy savings and durability. Hospitals, warehouses, and sports complexes benefit from the panels’ fire safety and noise reduction. Builders choose these panels for fast installation and long-term cost savings. A research facility for LG used insulated metal wall panels to achieve high energy efficiency and occupant comfort. The panels also support green building goals because they contain recycled materials and can be recycled at the end of their life.
Aluminum Exterior Wall Panels
Residential Applications
Homeowners and builders increasingly select aluminum exterior wall panels for residential projects. These panels offer a modern look, high durability, and low maintenance. Compared to traditional materials, aluminum exterior wall panels provide better fire and water resistance. They also weigh less, making installation easier and faster.
Feature | Wood | Stone | Concrete | ACP (Aluminum Composite Panels) |
---|---|---|---|---|
Moderate | High | Moderate | Moderate | |
Long-Term Cost | High | High | Moderate | Low |
Durability | Low | High | High | High |
Aesthetics | High | High | Moderate | High |
Weight | Low | High | High | Low |
Maintenance | High | Low | Low | Low |
Fire Resistance | Low | High | High | High |
Water Resistance | Low | High | High | High |
Aluminum exterior wall panels stand out for their environmental benefits. They use recyclable materials and help reduce energy use in homes. Market studies show that these panels meet the needs of modern families who want safe, attractive, and energy-efficient houses. New fire-retardant cores and eco-friendly coatings make them even safer and more sustainable. Their design flexibility allows for unique home exteriors and creative architectural styles.
Commercial Applications
Commercial building owners rely on aluminum exterior wall panels for performance and design flexibility. These panels protect buildings from harsh weather, fire, and impact. They also help lower energy costs by improving insulation and reducing heat loss.
- Aluminum exterior wall panels increase a building’s value by offering long-lasting durability and low maintenance.
- They support innovative designs, including curved and solar-integrated facades.
- Real-world projects, such as the Burj Khalifa and San Francisco Museum of Modern Art, show how these panels perform in demanding environments.
Commercial building projects benefit from the panels’ lightweight nature, which reduces structural load and speeds up installation. Experts highlight that aluminum exterior wall panels improve thermal performance and help buildings meet green standards like LEED and BREEAM. The panels’ recyclability rate exceeds 90%, making them a top choice for sustainable exterior cladding. Architects and engineers often choose these panels for their ability to meet strict safety, energy, and design requirements.
Tip: Aluminum exterior wall panels offer a smart solution for both new construction and renovation projects, helping commercial buildings stay competitive and efficient.
Best Wall Panels for Different Needs
Home Use
Selecting the best wall panels for a home involves balancing durability, style, insulation, and maintenance. Homeowners often seek materials that provide long-term value, safety, and visual appeal. The following table compares popular wall panel options for residential projects:
Material Type | Durability & Resistance | Maintenance Requirements | Aesthetics & Style | Insulation & Energy Efficiency | Installation & Cost Considerations |
---|---|---|---|---|---|
Fiber Cement Panels | Highly durable; fire-resistant; resists termites & mold | Minimal upkeep; difficult to cut; heavy | Mimics wood, stone, brick; suited for modern/industrial | Requires additional insulation; long lifespan (30-50 yrs) | Professional installation often needed; mid-range cost |
Metal Siding (Aluminum/Steel) | Durable; resistant to rot, pests, weather; prone to dents | Low maintenance; may need dent repairs | Modern, sleek, industrial aesthetic | Poor insulator; needs extra insulation layers | Requires corrosion-resistant fasteners; higher cost |
Vinyl Panels | Moisture resistant; prone to warping, cracking, fading | Easy to clean; DIY-friendly | Variety of colors and wood-look finishes | Needs additional insulation for energy efficiency | Budget-friendly; easy installation; lower durability |
Composite Wood Slat Panels | Weather-resistant; fire-resistant; pest-resistant | Minimal maintenance; no regular treatments | Realistic wood look; suits modern and rustic styles | Natural thermal regulation; improves indoor comfort | Slightly higher cost; straightforward installation |
Natural Wood Panels | Classic appeal; moisture and pest susceptible | Requires regular sealing/staining | Timeless, warm aesthetic | Provides insulation but less energy efficient | Installation varies; ongoing maintenance increases cost |
Homeowners who want a modern look and low maintenance often choose metal siding, especially aluminum wall panels. These panels resist rot, pests, and weather, making them a reliable choice for many climates. However, they can dent more easily than other materials and need extra insulation for energy efficiency. Fiber cement panels offer high durability and fire resistance, but their weight and cutting difficulty require professional installation.
Composite wood slat panels provide a realistic wood appearance with better weather and fire resistance than natural wood. They also help regulate indoor temperature, improving comfort in the home. Vinyl panels remain popular for their affordability and easy installation, but they may not last as long as other options.
Tip: For the best wall panels in a home, consider the local climate, desired style, and willingness to perform maintenance. Aluminum wall panels deliver a sleek, modern finish and long-term durability, especially when paired with proper insulation.
Commercial Use
Commercial buildings demand wall panels that combine performance, safety, and design flexibility. Owners and architects look for solutions that meet strict codes, reduce energy costs, and support branding or architectural goals. The table below highlights leading wall panel systems for commercial applications:
Wall Panel System | Key Benefits and Features | Considerations for Commercial Use |
---|---|---|
Insulated Metal Panel (IMP) | High insulation, energy efficiency, durability, weather resistance, aesthetic flexibility | Best for buildings needing strong insulation; suitable for energy-conscious projects; requires professional input |
Single Skin Profile Metal Panel | Low cost, simple installation, lightweight, various profiles | Suitable for budget-sensitive projects without insulation needs; less durable and minimal insulation |
Sleek modern look, fire and moisture resistant, customizable shapes, low maintenance | Ideal for high-end commercial buildings prioritizing aesthetics and durability; requires experienced installers |
Insulated metal panels stand out for their energy efficiency and weather resistance. These panels help commercial buildings maintain comfortable temperatures and reduce utility bills. Aluminum composite material panels offer a modern appearance, fire safety, and low maintenance, making them a top choice for offices, retail spaces, and institutional buildings. Single skin profile metal panels provide a cost-effective solution for projects with limited insulation needs.
Recent research shows that advanced insulation materials, such as vacuum insulation panels, can further improve energy performance in commercial buildings. These innovations support both economic and environmental goals by reducing heating and cooling costs while maximizing usable floor space.
Note: Commercial grade wall panels should match the building’s function, climate, and budget. Consulting with professionals ensures the best wall panels are selected for each unique project.
Metal Wall Panel vs. Other Materials
Aluminum vs. Wood
When comparing a metal wall panel to wood, several differences stand out. Aluminum panels resist moisture, pests, and fire, while wood panels can rot, warp, or attract insects. Builders often choose aluminum for its long lifespan and minimal maintenance. Wood panels require regular sealing or painting to prevent decay. In terms of strength, aluminum-laminated panels show much higher bending strength and edgewise shear strength than non-laminated wood panels. Wood-based panels may use more resin, which increases costs and environmental impact. Aluminum panels also offer better recyclability, making them a sustainable choice for modern construction.
Property | Metal Wall Panel (Aluminum) | Wood Panel |
---|---|---|
Durability | High | Moderate |
Maintenance | Low | High |
Fire Resistance | Excellent | Poor |
Recyclability | High | Limited |
Cost Over Time | Lower | Higher |
Aluminum panels provide a reliable solution for projects that need durability and low upkeep.
Aluminum vs. Phenolic
Phenolic panels, often reinforced with fiberglass and foam, have improved strength and stiffness compared to basic wood panels. However, these panels can still fail due to core buckling, which limits their use in demanding environments. A metal wall panel made from aluminum avoids these issues by offering better shear strength and flexural performance. Aluminum panels also reduce resin consumption by over 40%, lowering production costs. Phenolic panels may not match the durability or recyclability of aluminum. For projects that require long-term reliability, aluminum panels deliver a clear advantage.
Aluminum vs. Steel
Steel panels are known for their high strength and stiffness, but they weigh much more than aluminum. This extra weight increases installation effort and structural load. A metal wall panel made from aluminum is lighter, which makes handling and installation easier. Aluminum also resists corrosion better than steel, especially in humid or coastal areas. While steel panels offer greater stiffness, aluminum panels provide a better balance of durability, weight, and recyclability. Research shows that foam-filled steel tubes improve energy absorption, but aluminum panels still offer a more efficient recycling process and lower risk of corrosion. Impact tests reveal that aluminum panels can predictably absorb energy and resist damage, making them suitable for many building applications.
Choosing the right metal wall panel depends on project needs, but aluminum often stands out for its cost-effectiveness, ease of installation, and long-term performance.
Comparison Table
Choosing the right aluminum wall panel depends on many factors. Builders and architects often compare options based on cost, durability, appearance, installation, and best uses. The table below provides a side-by-side comparison of the most common types. This helps readers quickly see which panel fits their project needs.
Panel Type | Cost Range (per m²) | Durability & Weather Resistance | Aesthetics & Customization | Installation Complexity | Best Uses |
---|---|---|---|---|---|
$20 – $60 | Good; moderate fire rating (B1/A2) | Many colors, finishes, easy shapes | Simple | Facades, signage, interiors | |
Solid Aluminum Panel | $40 – $80 | Excellent; high fire & impact resistance | Sleek, modern, limited curves | Moderate | High-traffic exteriors, canopies, public areas |
Corrugated Aluminum Panel | $25 – $50 | Strong; resists corrosion, wind | Industrial, modern look | Easy | Warehouses, schools, utility buildings |
Perforated Aluminum Panel | $30 – $70 | Good; needs proper coating for outdoors | Custom patterns, light control | Moderate | Sunscreens, facades, partitions |
Honeycomb Aluminum Panel | $50 – $120 | Superior; lightweight, high strength | Flat, clean, large panels possible | Complex | Curtain walls, airports, large facades |
Insulated Metal Panel | $35 – $90 | Excellent; top insulation, fire safe | Smooth, modern, color options | Moderate | Energy-efficient buildings, hospitals, offices |
Tip: For exterior projects, thicker panels and advanced PVDF coatings improve weather resistance and color retention. In coastal or industrial zones, 5052 alloy and three-coat PVDF systems offer the best protection.
A comparison of aluminum cladding types shows that each panel serves a unique purpose. Interior panels focus on aesthetics and easy cleaning, while exterior panels require strength and weatherproofing. Aluminum cladding meets strict safety and environmental standards, making it a reliable choice for both homes and commercial buildings.
Scenario-based recommendations guide panel selection. For example, a hospital operating room benefits from anti-bacterial powder-coated panels, while a coastal high-rise needs thick, corrosion-resistant panels. This approach ensures the right balance of performance and appearance for every application.
Aluminum wall panels offer a range of options for modern construction. Each type brings unique strengths. Composite panels provide design flexibility. Solid panels deliver high durability. Corrugated panels suit industrial looks. Perforated and honeycomb panels add style and strength. Insulated panels improve energy efficiency.
For the best results, builders should match panel choice to project needs, budget, and design goals. Consulting with a supplier or architect ensures the right fit for both function and appearance.
FAQ
What is the lifespan of aluminum wall panels?
Most aluminum wall panels last 30 to 50 years. Manufacturers design them to resist corrosion, fading, and impact. Regular cleaning and inspections help extend their service life.
Are aluminum wall panels environmentally friendly?
Yes. Aluminum panels use recycled materials and can be recycled again after use. Many products meet green building standards and help reduce energy use in buildings.
Can aluminum wall panels be painted or refinished?
Manufacturers offer panels in many colors and finishes. If needed, professionals can repaint or refinish panels using approved coatings. Always follow manufacturer guidelines for best results.
How do aluminum wall panels perform in extreme weather?
Aluminum panels resist wind, rain, and temperature changes. Protective coatings prevent corrosion and fading. In hurricane zones, thicker panels and secure fasteners improve performance.
Do aluminum wall panels require special maintenance?
Most panels need only occasional cleaning with water and mild soap. Inspect fasteners and seals once or twice a year. Quick repairs keep panels looking and working their best.