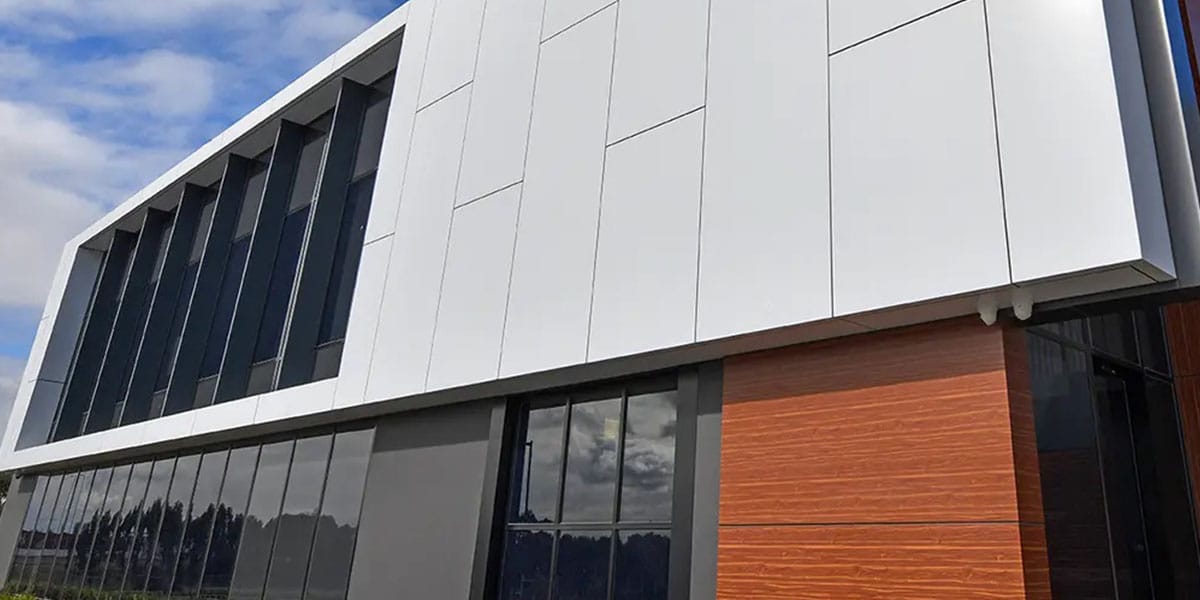
07 Jul Top PVDF Aluminum Composite Panel Manufacturers to Watch in 2025
Table of Contents
- 1 Key Takeaways
- 2 Leading PVDF Aluminium Composite Panel Manufacturers
- 3 What Sets Top Manufacturers Apart
- 4 Aluminium Composite Panel Product Comparison
- 5 How to Choose Aluminum Cladding Manufacturers
- 6 Aluminum Composite Panels Market Trends
- 7 FAQ
- 7.1 What makes PVDF aluminum composite panels different from other cladding materials?
- 7.2 How do manufacturers ensure the quality of aluminum composite panels?
- 7.3 Can aluminum composite panels be recycled?
- 7.4 What are the main applications for aluminum composite panels?
- 7.5 How should buyers select the right aluminum panel manufacturer?
Selecting the right manufacturers for PVDF aluminium composite panel projects in 2025 shapes project durability, safety, and design. Reliable aluminum cladding manufacturers drive success through advanced coatings, strict quality control, and global support. The market for aluminum composite panels continues to expand, showing strong demand for cladding solutions that offer superior performance.
Metric | Value | Significance |
---|---|---|
PVDF Market Share (2024) | 36.5% | Dominant coating type due to durability and resistance, highlighting importance of PVDF ACPs |
Global ACP Market Size (2024) | USD 6.6B | Large market size indicating high demand |
Market CAGR (2025-2033) | 4.7% | Steady growth forecast emphasizing expanding market |
Fire-resistant Panel Market Share (2024) | 55.2% | Emphasizes critical role of quality and safety compliance in manufacturing |
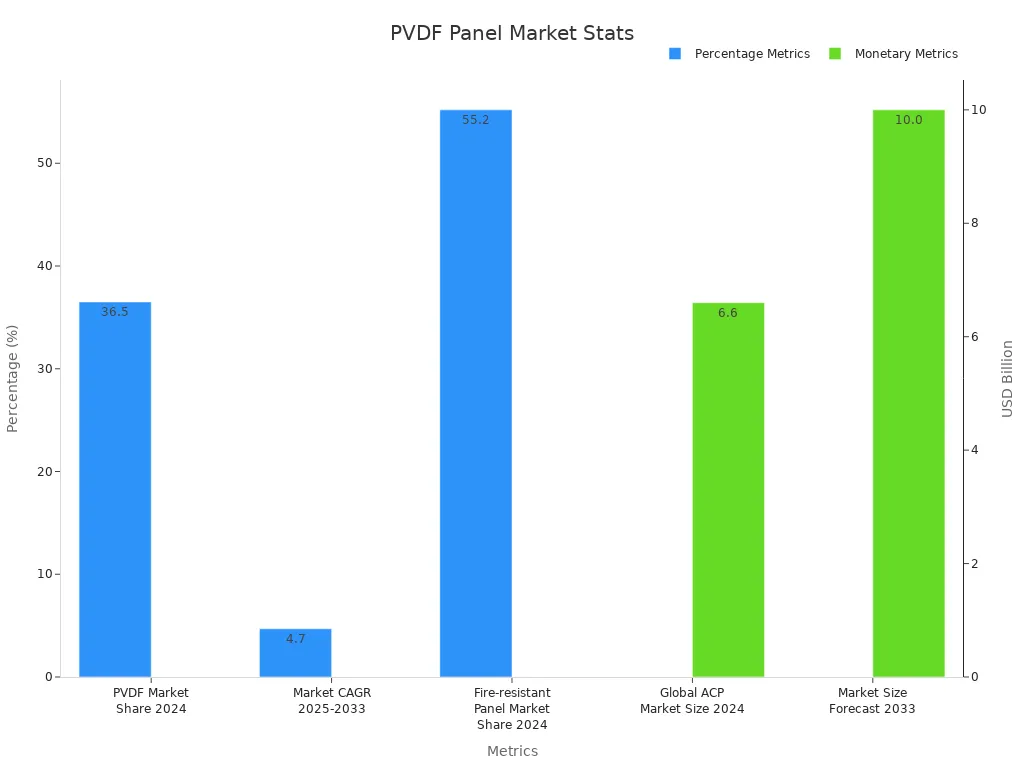
Global trends show that manufacturers invest in aluminum innovation, durability, and eco-friendly cladding. This commitment results in higher performance and safety, supporting architectural and construction excellence worldwide.
Key Takeaways
- Top PVDF aluminum composite panel manufacturers lead with strong product quality, advanced coatings, and reliable global support.
- Innovation and research drive better durability, weather resistance, and sustainability in aluminum composite panels.
- Customization options like colors and finishes help meet unique project needs and increase customer satisfaction.
- Strict quality standards and certifications ensure safety, fire resistance, and consistent performance of panels.
- Choosing manufacturers with proven after-sales support and sustainability practices leads to long-term project success.
Leading PVDF Aluminium Composite Panel Manufacturers
Alubond
Alubond stands as a global leader in the aluminium composite panel industry. The company expanded its UAE production facility in 2023 to meet rising demand for high-performance aluminum composite panels. Alubond focuses on smart cities and infrastructure projects, which require advanced cladding and facade solutions. The company developed fire-retardant A1 aluminium composite panels in 2020, which do not produce smoke and are non-combustible. These innovations help Alubond maintain a strong position in the market.
Metric | Details |
---|---|
Market size (2023) | |
Market size (2032 forecast) | USD 17.19 Billion |
CAGR (2025-2032) | 6.8% |
Notable innovation | Fire-Retardant A1 ACPs |
Market focus | Smart cities, infrastructure |
Alubond’s products offer excellent weather resistance and durability, making them ideal for exterior cladding and facade applications in harsh climates.
Alcadex
Alcadex delivers high-quality PVDF aluminium composite panels for architectural and industrial projects. The company invests in advanced coating technology to ensure long-lasting color and surface protection. Alcadex panels support a wide range of facade designs, from commercial buildings to modern residential complexes. The manufacturer emphasizes strict quality control and offers custom solutions for unique cladding requirements.
Alusign
Alusign specializes in aluminum composite panels with PVDF coatings. The company serves clients in over 80 countries, providing reliable cladding materials for both interior and exterior applications. Alusign’s panels resist corrosion and UV damage, which extends the lifespan of building facades. The company’s commitment to research and development leads to innovative products that meet global safety standards.
AluminoBond
AluminoBond produces aluminium composite panels with a focus on sustainability and performance. The manufacturer uses eco-friendly materials and advanced aluminum processing techniques. AluminoBond panels offer high impact resistance and flexibility, making them suitable for complex facade shapes. The company supports architects and builders with technical guidance and after-sales service.
Arconic
Arconic is a well-known name in the aluminum industry. The company supplies PVDF aluminium composite panels for iconic buildings and infrastructure projects worldwide. Arconic’s panels provide superior fire resistance and weather protection, which are essential for modern cladding systems. The company’s global network ensures timely delivery and technical support for large-scale facade projects.
Alumax
Alumax Industrial, based in Taiwan, ranks among the top competitors in the PVDF aluminium composite panel market. The company appears in major industry reports alongside global leaders such as Arconic and Mitsubishi Chemical. Alumax’s financial performance and market share reflect its reliability and strong presence in the aluminum composite panels sector. The manufacturer offers a wide range of cladding solutions for commercial and residential facades.
- Alumax’s inclusion in competitor analysis sections highlights its dependable reputation.
- The company’s revenue share by segment and region demonstrates its reach in the global market.
- Alumax supports sustainable building practices through innovative aluminum processing.
Pivot
Pivot manufactures aluminium composite panels with a focus on precision and quality. The company’s PVDF-coated panels resist fading and weathering, which makes them suitable for exterior cladding and facade systems. Pivot offers a variety of colors and finishes to meet the needs of architects and designers. The manufacturer’s customer service team provides technical support throughout the project lifecycle.
Seven
Seven is recognized for its advanced aluminum composite panels and commitment to innovation. The company invests in research and development to improve panel performance and sustainability. Seven’s PVDF aluminium composite panels are used in commercial, educational, and healthcare buildings. The manufacturer’s products meet international safety and environmental standards, making them a trusted choice for modern cladding and facade projects.
CCJX
CCJX supplies aluminium composite panels for a wide range of applications, including high-rise buildings and public infrastructure. The company’s PVDF-coated panels offer excellent durability and color retention. CCJX focuses on quality assurance and continuous improvement, which helps maintain its reputation among leading manufacturers. The company supports architects and builders with design consultation and after-sales service.
Note:
Several key manufacturers, including Alubond, Arconic, Alumax, and others, lead the PVDF aluminium composite panel market in 2025. Their focus on innovation, quality, and global support drives the adoption of aluminum composite panels for cladding and facade applications in commercial and high-rise buildings. Rapid urbanization and infrastructure growth in regions like Asia-Pacific further strengthen their market leadership.
What Sets Top Manufacturers Apart
Product Quality
Top aluminum composite panel manufacturers set themselves apart through strict quality standards and certifications. They use ISO 9001:2015 and ISO 13485:2016 certifications to ensure consistent product quality. Many operate ISO Class 7 and ISO Class 8 cleanroom facilities, which help maintain clean manufacturing environments. These companies focus on exceeding customer expectations by involving suppliers, employees, and distribution networks in their quality policies. They use supplier audits, material verification, and operator training to deliver high durability and reliable performance.
Aspect | Details |
---|---|
Quality Standards | ISO 9001:2015, ISO 13485:2016 |
Cleanroom Certifications | ISO Class 7, ISO Class 8 (ISO 14644-1) |
Quality Policy | Exceed customer expectations, involve all stakeholders |
Supplier Quality | Audits, material verification, partnership for issue resolution |
Operations Quality | Cleanroom protocols, automation, Statistical Process Controls |
Customer Quality | Fast complaint response, failure analysis, trend monitoring |
Certificates | ISO 13485:2016, ISO Class 7 and 8 cleanroom certificates available |
Innovation and R&D
Manufacturers invest heavily in research and development to improve aluminum panel performance. The top 1,000 global companies account for 40% of all R&D spending, with corporate R&D investments reaching about USD 1.2 trillion in 2023–2024. These investments support the development of new PVDF and FEVE coating technologies, which boost weather resistance and color retention. Companies also track patent filings and scientific publications to measure innovation output. This focus on R&D leads to better performance, sustainability, and safety for high-performance building envelope solutions.
Evidence Type | Details & Figures |
---|---|
Global R&D Expenditure Growth | 2022 growth slowed to 5% (real terms), down from 6.6% in 2021; business R&D growth slowed to 6% in 2022 (from 8.5%). |
Corporate R&D Spending | Top corporate R&D spenders invested around USD 1.2 trillion in 2023–2024, with 8.3% nominal and 6.1% real growth. |
Patent Filings | International patent applications via WIPO Patent Cooperation Treaty reflect innovation output. |
Customization
Customization plays a key role in aluminum composite panel selection. Manufacturers offer a wide range of colors, finishes, and sizes to meet unique project needs. Personalization drives customer satisfaction and loyalty. For example, 71% of consumers are willing to pay more for personalized products, and 80% prefer brands that offer customization. Companies that use preference-based personalization see a 20% increase in sales and a 15% boost in customer retention.
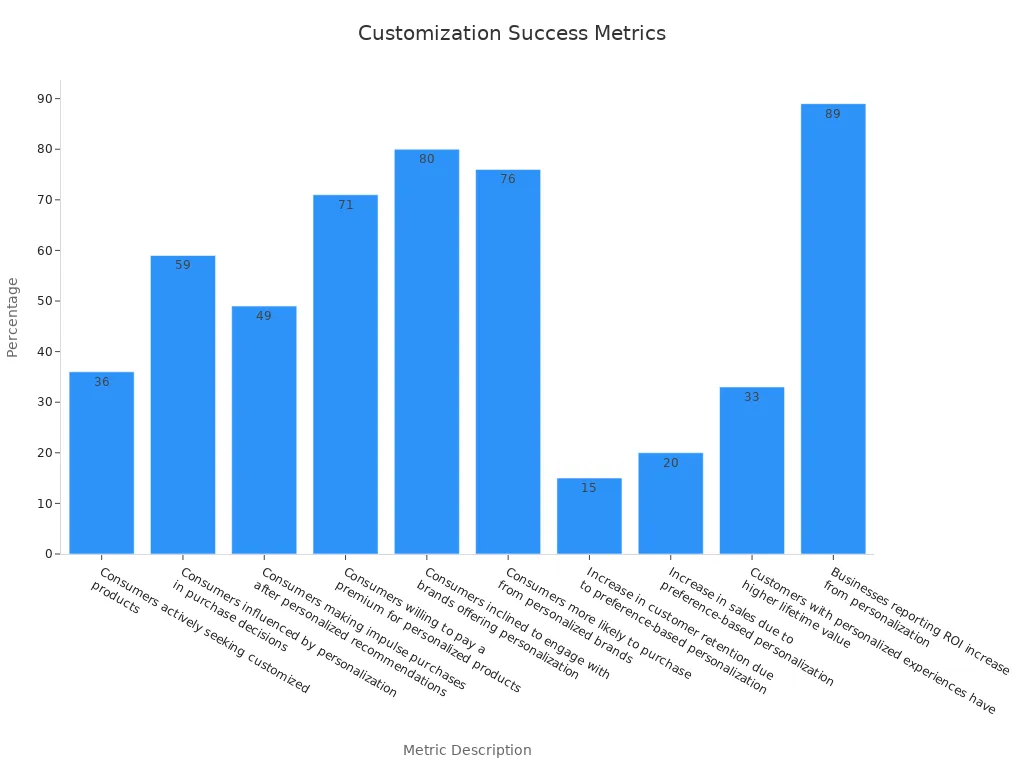
Metric Description | Statistic/Percentage |
---|---|
Consumers actively seeking customized products | 36% |
Consumers influenced by personalization in purchase decisions | 59% |
Consumers making impulse purchases after personalized recommendations | 49% |
Consumers willing to pay a premium for personalized products | 71% |
Increase in customer retention due to preference-based personalization | 15% |
Increase in sales due to preference-based personalization | 20% |
Global Support
Global support ensures that aluminum panel manufacturers can serve projects worldwide. Leading companies maintain regional service centers and authorized partners to provide fast, reliable assistance. Customer satisfaction ratings for phone support reach 91%, while live chat support scores 85%. Customers value knowledgeable agents, quick response times, and being treated as valued clients. Companies with strong global support networks achieve high service quality ratings and excellent Net Promoter Scores, which reflect customer loyalty and recommendation rates.
Support Channel | Customer Satisfaction Rating | Additional Insight |
---|---|---|
Phone Support | 91% | Highest satisfaction, preferred for complex issues |
Live Chat Support | 85% | High satisfaction, real-time assistance |
Preference for Voice Calls | 88% | Customers prefer live agents over automated menus |
Real-time Support Impact | 63% of companies report increased brand loyalty | Demonstrates value of immediate support |
Companies that combine high durability, advanced performance, and strong customer support stand out in the aluminum composite panel market.
Aluminium Composite Panel Product Comparison
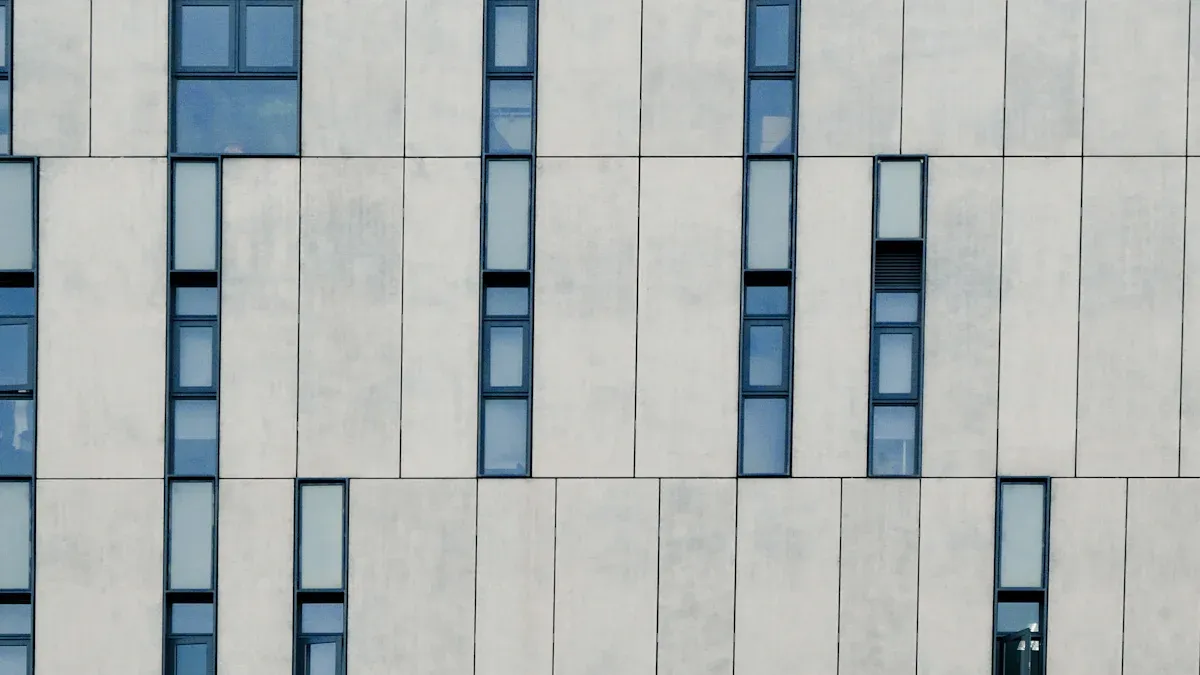
PVDF Coating Features
PVDF coatings play a key role in the performance of aluminium composite panels. Manufacturers use different resin contents, with 70% PVDF resin-based coatings providing the best durability and chemical resistance. Some brands, such as Hylar and Kynar, offer similar weathering performance. Product differences often come from film thickness, color options, and additives that improve durability. Pigment types, including organic, inorganic, and pearlescent, affect color stability and long-term appearance. Many companies now focus on eco-friendly innovations, such as water-based and low-VOC coatings, to meet environmental standards. Pricing varies based on resin quality, pigment selection, and special features like self-cleaning or anti-graffiti properties. These factors help architects and builders select the right pvdf aluminium composite panel for each project.
Durability and Performance
Aluminium composite panels must pass strict durability and performance tests. Fatigue testing measures how panels handle repeated stress over time. Environmental tests check how moisture and temperature changes affect the panels. Non-destructive methods, such as acoustic emission and thermography, monitor damage during use. Manufacturers also analyze failure modes to understand how panels react under different conditions. Moisture absorption and heat aging tests show how panels perform in real-world environments. These tests ensure that aluminum composite panels offer high durability and reliable performance for cladding and facade systems. Statistical analysis helps companies compare results and improve product quality.
Application Scenarios
Aluminium composite panels serve many roles in modern construction. Builders use them for exterior cladding, interior walls, and decorative facade elements. The panels provide a lightweight yet strong solution for high-rise buildings, shopping centers, and airports. Their high durability and weather resistance make them ideal for harsh climates. In addition, the panels support creative designs with a wide range of colors and finishes. A life cycle assessment shows that aluminum composite panels have lower environmental impacts than some alternatives, such as carbon fiber composites. This advantage comes from a high recycling rate and lower energy use during recycling. Architects choose pvdf aluminium composite panel products for projects that demand both performance and sustainability.
How to Choose Aluminum Cladding Manufacturers
Key Criteria
Selecting the right aluminum cladding manufacturers requires careful evaluation of several factors. Quality certifications such as ISO 9001:2015 and EN 13501-1 for fire safety show a manufacturer’s commitment to safety and reliability. Regular quality audits, both internal and external, help maintain high standards. Manufacturers should also provide clear documentation and digital compliance tools to ensure transparency.
Criteria / Benchmark Category | Specific Evidence / Benchmark |
---|---|
Recycled Content | Novelis: 72% recycled aluminum; European suppliers: 75-95% recycled aluminum reducing embodied carbon by up to 50% |
Fire Safety Standards | EN 13501-1 (Europe), NFPA 285 (USA), BS 8414 (Singapore), National Construction Code (Australia) |
Sustainability Certifications | LEED v4.1, BREEAM, WELL, Cradle to Cradle Certified |
Innovation & Technology | Nano-ceramic coatings, digital customization platforms |
Lifecycle Cost Analysis | 62% lower maintenance costs over 40 years compared to precast concrete |
Tip: Request product samples and review test certificates before making a final decision.
Cost Factors
Aluminum prices change by region and market trends. North America averages US$2.42 per kilogram, while Northeast Asia reaches US$2.74 per kilogram. These prices reflect supply, demand, and raw material costs. Manufacturers who localize production can offer better pricing and faster delivery.
- Immediate cost drivers include feedstock prices and market futures.
- Lifecycle cost analysis shows aluminum cladding systems reduce maintenance costs by 62% over 40 years compared to alternatives.
- Use supplier pricing indices to compare offers and ensure cost efficiency.
Environmental Considerations
Sustainability plays a major role in choosing aluminum cladding manufacturers. Many companies now use recycled aluminum, with some products containing over 95% post-consumer scrap. Recycling aluminum uses 95% less energy than producing new material, which lowers carbon emissions.
Product Name | Sustainability Highlights | Advantages | Typical Use Cases |
---|---|---|---|
Contains >95% post-consumer scrap; fully traceable and third-party verified | High recycled content; versatile applications | Roofing, facades; automotive panels | |
Hydro Aluminum Foundry Alloy | Low-emission production; EPD certified | High metal quality; reduced environmental footprint | Automotive components; industrial casting |
Note: Look for Environmental Product Declarations (EPDs) and certifications like LEED or BREEAM to confirm a manufacturer’s sustainability claims.
After-Sales Support
Strong after-sales support ensures long-term satisfaction with cladding and facade systems. Leading aluminum cladding manufacturers track customer satisfaction using metrics such as CSAT, Net Promoter Score, and First Contact Resolution rate. High-performing companies resolve most issues on the first contact and maintain fast response times.
Metric Name | Description | Significance in After-Sales Support |
---|---|---|
Measures immediate feedback on support interactions. | Shows if customer expectations are met. | |
Net Promoter Score (NPS) | Measures customer loyalty and likelihood to recommend. | Reflects long-term satisfaction. |
First Contact Resolution (FCR) Rate | Percentage of issues resolved in the first interaction. | Higher rates increase satisfaction. |
Service Level Agreement (SLA) Compliance | Measures adherence to agreed service standards. | Ensures timely, high-quality support. |
Tip: Choose manufacturers with a proven track record of responsive support and clear service agreements.
Aluminum Composite Panels Market Trends
The aluminum composite panels market continues to show strong growth worldwide. Companies see rising demand for cladding and facade solutions in both new construction and renovation projects. The market reached USD 6.47 billion in 2024 and is forecast to grow to USD 9.65 billion by 2030, with a CAGR of 7.0%. Asia Pacific leads with over 40% market share, driven by rapid urbanization and infrastructure development. Italy shows the highest regional growth rate, while North America holds a 26.8% revenue share due to green building and infrastructure programs.
Metric/Aspect | Value/Detail |
---|---|
Market Size 2024 | USD 6,468.1 million |
Market Size 2030 (Forecast) | USD 9,648.0 million |
CAGR (2025-2030) | 7.0% |
Largest Regional Market (2024) | Asia Pacific (40.8% market share) |
Leading Product Segment | PVDF segment (36.1% revenue share in 2024) |
Dominant Application Segment | Construction (54.0% revenue share in 2024) |
North America Revenue Share | 26.8% (2024) |
Lightweight, high insulation, durability, flexibility, sealing, air/water barriers |
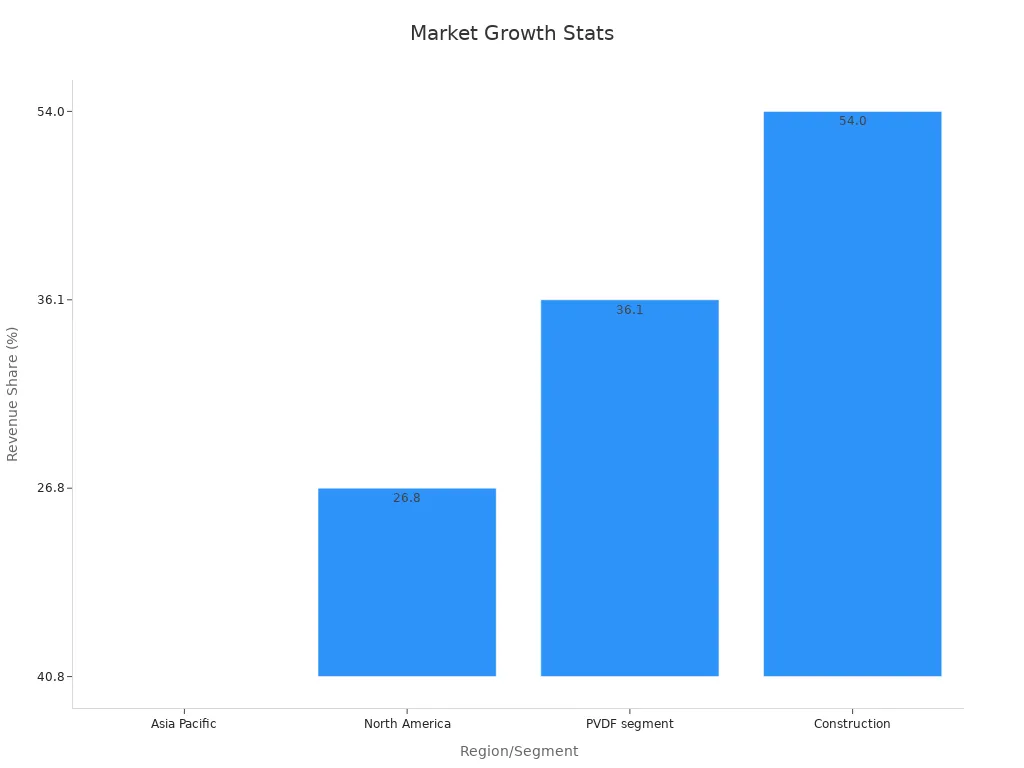
Manufacturers focus on improving aluminum panel performance for cladding and facade applications. They invest in new coating technologies and expand production capacity. PVDF panels remain the top choice for durability and corrosion resistance. Builders prefer these panels for their lightweight structure and high insulation, which help create energy-efficient buildings.
Regional segmentation highlights Asia Pacific as the largest market, followed by North America and Europe. Growth in Asia Pacific comes from government initiatives and affordable housing schemes. North America and Europe benefit from strict energy efficiency regulations and green building trends. Companies like Arconic, Mitsubishi, and Alubond USA lead the market with innovative aluminum cladding products.
Market analysts use tools such as Porter’s Five Forces and SWOT to track competition and identify growth opportunities. They note that demand for advanced facade systems and sustainable cladding drives ongoing investment in research and development.
The construction segment dominates with a 54% revenue share, but transportation and advertising also see expanding use of aluminum composite panels. Builders choose these panels for their flexibility, sealing ability, and reliable performance in harsh environments. Regulatory support, such as LEED and British Safety Standards, encourages the use of lightweight, high-performance cladding and facade materials.
Top PVDF aluminium composite panel manufacturers lead the industry with strong aluminum product quality, advanced aluminum coating technology, and reliable aluminum support services. They invest in aluminum innovation and offer aluminum solutions for many project needs. Each company provides aluminum panels with excellent durability and design flexibility. Readers should compare aluminum options, review aluminum certifications, and request aluminum samples. Contacting aluminum suppliers helps ensure the right aluminum choice for every project.
FAQ
What makes PVDF aluminum composite panels different from other cladding materials?
PVDF aluminum composite panels offer high durability, weather resistance, and color stability. These panels use advanced coatings that protect buildings from harsh environments. Many architects choose aluminum for its lightweight structure and long-lasting performance.
How do manufacturers ensure the quality of aluminum composite panels?
Manufacturers use strict quality control systems and international certifications. They test aluminum panels for strength, fire safety, and weather resistance. Regular audits and advanced production methods help maintain consistent quality across all aluminum products.
Can aluminum composite panels be recycled?
Yes, aluminum composite panels are highly recyclable. Many manufacturers use recycled aluminum in their products. Recycling aluminum saves energy and reduces environmental impact, making it a sustainable choice for modern construction projects.
What are the main applications for aluminum composite panels?
Builders use aluminum composite panels for exterior cladding, interior walls, signage, and decorative facades. These panels provide flexibility in design and suit both commercial and residential buildings. Aluminum panels also work well in transportation and industrial projects.
How should buyers select the right aluminum panel manufacturer?
Buyers should check for certifications, product warranties, and after-sales support. Comparing aluminum panel samples and reviewing customer feedback helps identify reliable suppliers. Strong technical support and transparent documentation also indicate a trustworthy aluminum manufacturer.