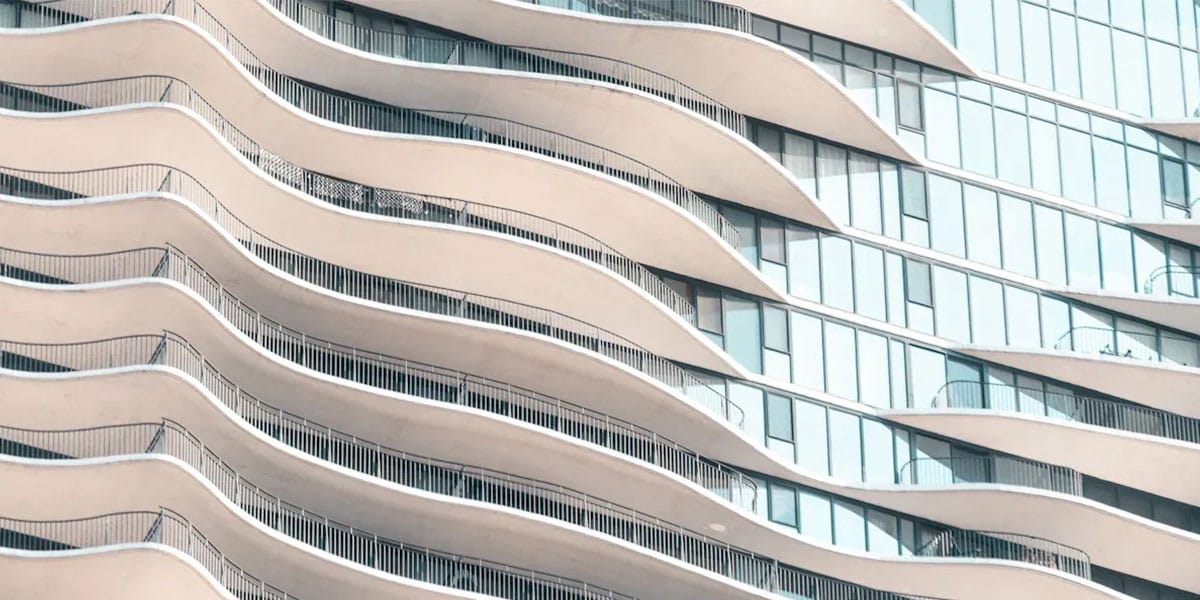
05 Jul Aluminum Wall Panels vs Other Cladding Options in 2025
Table of Contents
Aluminum panels for walls lead the market in 2025. Many builders choose aluminum cladding because it combines strength, durability, and modern style. Aluminum siding outpaces other cladding options in growth and value. The table below shows how aluminum panels and metal panels dominate the industry:
Metric/Aspect | Aluminum Cladding (2025) | Other Wall Cladding Materials |
---|---|---|
Market Size | USD 8.5 billion (2023) | |
CAGR (2025-2034) | 6.8% | 4.5% |
Aluminum siding resists rust and weather better than wood or vinyl. Metal panels like aluminum siding also weigh less, making installation faster. However, aluminum panels for walls may dent more easily than stone. Each project needs careful review of cost, durability, maintenance, style, and environmental impact.
Key Takeaways
- Aluminum wall panels offer strong durability, resist rust, and need little maintenance, making them ideal for harsh weather and long-lasting use.
- These panels are lightweight and easy to install, which saves time and labor costs on building projects.
- Aluminum cladding supports energy efficiency by improving insulation, helping lower heating and cooling bills.
- Design options for aluminum panels are versatile, with many colors, shapes, and finishes to fit modern and classic building styles.
- Aluminum panels are recyclable and meet strict safety codes, supporting sustainable building and fire safety requirements.
Cladding Overview
What Is Cladding
Cladding refers to the layers or panels attached to the outside of a building. These layers do not support the building’s weight. Instead, they protect the structure from wind, rain, heat, and other environmental factors. Cladding systems can include insulation, membranes, and fixings that help keep buildings dry and energy efficient. Builders use cladding to improve both the look and performance of a building.
Modern cladding comes in many forms. Some common types include metal panels, wood siding, brick veneer, stone veneer, and rainscreen systems. Each type offers unique benefits. For example, metal cladding is popular in commercial and industrial buildings because it is durable and recyclable. Wood siding is often chosen for custom homes due to its natural appearance. Rainscreen systems add an extra layer of protection by allowing air to flow behind the panels, which helps prevent moisture buildup.
Note: In the United States, cladding systems must meet strict building codes such as the International Building Code (IBC), NFPA 285 for fire safety, and ASTM standards for wind and water resistance. These rules help ensure that cladding protects buildings in all kinds of weather.
Material Type | Common Use Cases | Key Features |
---|---|---|
Metal Cladding | Commercial, industrial, institutional | Durable, weather resistant, recyclable |
Wood Siding | Custom homes, heritage, high-end homes | Natural look, needs regular maintenance |
Brick/Stone Veneer | Residential, institutional | Long-lasting, low maintenance, thermal mass |
Rainscreen Systems | LEED/passive buildings | Moisture control, energy efficiency |
Curtain Wall Systems | High-rise, commercial | Daylighting, acoustic performance, non-structural |
Why Material Choice Matters
Choosing the right cladding material affects a building’s safety, energy use, and lifespan. Builders must consider how each material performs in different climates and under local regulations. For example, after recent fire incidents, many countries now require non-combustible materials for taller buildings. This change has led to more use of metal and mineral-based cladding.
Material choice also impacts the environment. Using recyclable or renewable materials, such as metal or wood, can lower a building’s carbon footprint. Life cycle assessments show that careful selection of cladding can reduce emissions and waste. Builders who select durable materials help extend the life of buildings and reduce the need for repairs or replacements.
When comparing exterior wall panel options, it is important to look at durability, maintenance, and environmental impact. The right cladding can make a building safer, more attractive, and more sustainable for years to come.
Durability: Aluminum Panels for Walls
Metal vs Other Materials
Durability stands as a top concern when choosing wall cladding. Aluminum panels for walls offer a strong balance of strength and lightness. Metal panels, especially solid aluminum cladding, resist many types of damage. Builders often compare aluminum cladding to steel, wood, stone, fiber cement, vinyl, and phenolic panels.
- Steel: Steel metal panels provide high impact strength. However, steel can rust if not coated well. Aluminum panels do not rust, which gives them an edge in wet climates. Solid aluminum cladding also weighs less than steel, making it easier to handle.
- Wood: Wood cladding gives a natural look but needs regular care. Wood can rot, warp, or attract insects. Aluminum panels for walls do not face these problems. They keep their shape and color for many years.
- Stone: Stone veneer lasts a long time and resists dents. However, stone is heavy and hard to install. Aluminum composite cladding offers a lighter option with good durability. Metal panels can dent more easily than stone, but they do not crack.
- Fiber Cement: Fiber cement panels resist fire and pests. However, they can absorb water and may crack over time. Aluminum composite metal panels have better water resistance and do not swell or split.
- Vinyl: Vinyl siding costs less but can fade, crack, or warp in harsh weather. Metal cladding, such as solid aluminum cladding, keeps its look and strength much longer.
- Phenolic Panels: Phenolic panels resist moisture and UV rays. However, they may not match the fire resistance or lifespan of solid aluminum cladding.
Note: Metal panels, especially solid aluminum cladding, often meet strict fire codes. This makes them a safe choice for many buildings.
The table below shows how different cladding materials compare in key durability factors:
Material | Rust Resistance | Dent Resistance | Water Resistance | Life Expectancy | Weight |
---|---|---|---|---|---|
Solid Aluminum Cladding | Excellent | Good | Excellent | 40+ years | Light |
Steel Metal Panels | Good | Excellent | Good | 30-50 years | Heavy |
Wood Cladding | Poor | Fair | Poor | 10-20 years | Medium |
Stone Veneer | Excellent | Excellent | Excellent | 50+ years | Very Heavy |
Fiber Cement Panels | Good | Good | Fair | 25-40 years | Heavy |
Vinyl Siding | Excellent | Poor | Good | 15-25 years | Light |
Phenolic Panels | Good | Good | Good | 20-30 years | Medium |
Longevity and Resistance
Solid aluminum cladding stands out for its long life and strong resistance to many threats. Aluminum panels for walls do not rust, even in coastal or humid areas. This makes them a top choice for buildings that face rain, snow, or salt air. Metal panels, especially solid aluminum cladding, also resist UV rays, so colors stay bright for years.
Aluminum composite panels use a core material between two thin aluminum sheets. These aluminum composite metal panels weigh less than solid aluminum cladding but still offer good durability. The aluminum composite panel facade gives buildings a modern look and strong protection. Aluminum composite cladding resists water and chemicals, which helps prevent stains and corrosion. Builders often choose aluminum composite sheets for projects that need both style and strength.
Solid aluminum cladding can handle impacts better than many other metal panels. However, it may dent if hit hard. Stone and steel metal panels resist dents better, but they weigh more and cost more to install. Aluminum panels for walls offer a good balance between strength and weight.
Aluminum composite cladding also stands up well to fire. Many aluminum composite panels meet strict fire safety codes. This makes them a safe choice for tall buildings and public spaces. Metal cladding, such as solid aluminum cladding, does not attract mold or pests. This adds to its durability and keeps maintenance low.
Tip: For the longest life, builders should choose solid aluminum cladding with a high-quality finish. This finish adds extra protection against scratches and fading.
Maintenance Needs
Cleaning and Upkeep
Aluminum panels stand out for their easy maintenance. Most building owners clean these panels with mild, pH-neutral detergents and water. This simple process removes dirt and keeps the panels looking new. Solid aluminum cladding rarely needs more than a gentle wash. Owners should inspect seals and joints every few years to prevent leaks. Coating adhesion testing every two to three years helps maintain the finish and ensures long-term durability.
Other cladding materials often require more work. Wood siding needs regular painting and sealing. Fiber cement panels may need patching or repainting. Vinyl can crack or fade, which means more frequent repairs. Solid aluminum cladding avoids these problems. The panels resist stains and do not attract mold or pests. Many famous buildings, such as The Shard in London and One Central Park in Sydney, use aluminum panels because they keep their appearance with little effort.
Tip: Regular cleaning and quick inspections help solid aluminum cladding last for decades.
Weather and Corrosion
Solid aluminum cladding offers excellent corrosion resistance. These panels do not rust, even in coastal or humid areas. Builders choose aluminum panels for projects that face rain, snow, or salt air. The panels protect buildings from water infiltration and weather damage. Compared to galvanized steel, wood, stucco, and vinyl, aluminum panels provide much better corrosion resistance.
Solid aluminum cladding also stands up to harsh sunlight. The finish resists fading and chalking. Owners do not need to worry about tarnishing or dings from normal weather. In contrast, steel can rust, and wood can rot or warp. Vinyl may crack in extreme temperatures. Solid aluminum cladding keeps its shape and color for 40 to 50 years with minimal upkeep.
Cladding Material | Corrosion Resistance | Maintenance Level | Typical Lifespan |
---|---|---|---|
Solid Aluminum Cladding | Excellent | Low | 40-50 years |
Steel | Fair | Moderate | 30-50 years |
Wood | Poor | High | 10-20 years |
Fiber Cement | Good | Moderate | 25-40 years |
Vinyl | Fair | Moderate | 15-25 years |
Solid aluminum cladding remains a top choice for builders who want long-lasting, low-maintenance protection. The panels’ superior corrosion resistance and easy upkeep make them ideal for both commercial and residential projects.
Cost Comparison
Initial Costs
Builders often compare the price of aluminum wall panels to other cladding options before starting a project. Aluminum composite panels usually have a lower price than solid aluminum or steel. The price for aluminum composite panels can be higher than some wood types, but it is often less than steel. Solid aluminum panels have the highest initial price among metal options. Wood prices vary, but treated hardwoods can match or exceed the price of aluminum composite panels. Steel panels cost more upfront and need extra insulation, which increases the total price.
The table below shows typical initial price ranges for popular cladding materials:
Material | Initial Price (per sq ft) | Durability (Years) |
---|---|---|
Aluminum Composite Panels | Moderate | |
Solid Aluminum | High | 40-80 |
Steel | High | 50-100 |
Wood | Varies | 20-100+ |
EIFS | $14 – $22 | 30-50 |
James Hardie | $12 – $18 | 30-50 |
Note: The initial price does not include installation or insulation for all materials.
Long-Term Value
The long-term value of cladding depends on maintenance, durability, and energy savings. Aluminum panels require little upkeep, which keeps long-term costs low. Steel panels need regular care to prevent rust, raising maintenance costs. Wood needs painting and sealing, which adds to the total price over time. EIFS and fiber cement panels also need regular checks and repairs.
Aluminum composite panels offer good thermal insulation, which can lower energy bills. Solid aluminum panels need extra insulation, but they last for decades with minimal care. The table below compares long-term costs and value additions:
Material | 30-Year Maintenance Cost | Energy Savings / Value Additions |
---|---|---|
Aluminum Composite Panels | Low | Good insulation, lower energy bills |
Solid Aluminum | Low to Moderate | Needs added insulation |
Steel | High | Poor insulation, extra insulation needed |
Wood | Moderate to High | Natural insulation, but high upkeep |
EIFS | $200-$500 annual energy savings | |
James Hardie | $9,700 | Minimal direct energy savings |
Aluminum cladding stands out for its balance of price, durability, and low maintenance. Builders often choose it for projects that need long-lasting value and predictable costs.
Aesthetics and Flexibility
Design Options
Aluminum wall panels give architects and builders many ways to shape a building’s look. These panels come in several types, such as metal composite material panels, single-skin panels, plate panels, perforated metal panels, and insulated panels. Each type offers unique design features. For example, plate panels allow for curves, tapers, and even perforations. Perforated metal panels often appear on accent walls, where custom patterns create a special visual effect.
The table below shows how different panel types support creative design:
Panel Type | |
---|---|
Metal Composite Material Panels | Painted or natural finishes; lightweight; prevents oil canning; smooth appearance |
Single Skin Metal Wall Panels | Concealed or exposed fasteners; horizontal or vertical installation; sleek, modern look |
Plate Panels | Allows curves, depths, perforations, and tapers; creates memorable façades |
Perforated Metal Panels | Customizable patterns; adds flair to accent walls |
Insulated Panels | Combines function and design flexibility; often used with other panel types |
Aluminum panels can form flat, curved, or even three-dimensional shapes. Builders use them on both modern and classic buildings. The Kendeda Building in Atlanta uses bare metal panels with different profiles to create shading and visual interest. At Calgary International Airport, over 800,000 square feet of metallic cladding show how color and form can work together on a large scale.
Color and Finish
Color and finish choices for aluminum wall panels are almost endless. Manufacturers offer metallic colors like Medium Grey and Champagne, as well as bare metal finishes. These panels can reflect light, which adds depth and vibrancy to a building’s facade. Some panels use special coatings to keep colors bright for many years.
Aluminum composite panels stand out for their consistent color and smooth finish. Builders can mix and match colors to fit any architectural style. These panels also work well with other materials, such as stone or brick, to create mixed-material facades. The reflective properties of aluminum panels help buildings look lively and modern, especially when sunlight changes throughout the day.
Tip: Choosing the right color and finish can make a building memorable and help it fit into its surroundings.
Environmental Impact
Sustainability
Sustainability plays a big role in choosing wall cladding. Aluminum cladding, especially aluminum composite panels, starts with a high energy demand. The process of making aluminum uses a lot of energy and can cause greenhouse gas emissions. Mining bauxite for aluminum can also lead to deforestation and loss of animal habitats. However, aluminum cladding lasts a long time. Its durability means builders do not need to replace it often, which helps reduce waste.
Recycling helps improve the sustainability of aluminum panels. Recycling aluminum uses much less energy than making new aluminum. New recycling methods, like semi-direct and direct recycling, lower emissions even more. Many experts say recycling is the best way to manage aluminum waste. Using recycled aluminum in cladding can cut down the carbon footprint of a building. Proper care and maintenance also help panels last longer, which supports sustainability.
Note: Life cycle assessments show that using recycled aluminum and keeping panels in good shape both help the environment.
Energy Efficiency
Energy efficiency is a key benefit of aluminum wall panels. These panels help keep buildings warm in winter and cool in summer. Aluminum composite panels add insulation and reduce thermal bridging. This means less heat escapes in winter and less heat enters in summer. As a result, buildings use less energy for heating and cooling.
Aluminum cladding improves energy efficiency by acting as a barrier against outside temperatures. Builders can choose panels with special coatings or extra insulation to boost energy efficiency even more. Over time, the energy savings from better energy efficiency can balance out the higher energy used to make the panels. Studies show that aluminum cladding can help lower energy bills and improve building performance.
A table below shows how aluminum cladding compares to other materials for energy efficiency:
Cladding Material | Energy Efficiency | Insulation Value | Impact on Energy Bills |
---|---|---|---|
Aluminum Composite Panels | High | Good | Lower |
Solid Aluminum | Moderate | Needs extra | Moderate |
Stone Veneer | Low | Poor | Higher |
Wood | Moderate | Good | Moderate |
Aluminum wall panels support both sustainability and energy efficiency. Builders who focus on these factors help create greener, more cost-effective buildings.
Installation: Aluminum Cladding Systems
Speed and Ease
Aluminum cladding systems help builders finish projects faster than many other cladding options. These systems use lightweight panels that are easy to move and lift. Many panels arrive at the job site already cut and finished, which saves time. Builders can install large sections in a single pass, reducing the number of steps needed.
A retrofit project in Cambridge, Massachusetts, showed how aluminum cladding systems can speed up work. Workers completed about 70% of the panel fabrication offsite. They installed the rest onsite using mast climbers. This method allowed for quick and precise placement, even on buildings with uneven surfaces. The Hyatt Regency Hotel project also used insulated metal panels (IMPs) to combine six wall layers into one. This reduced labor and waste, making installation much faster.
Project/Aspect | Installation Advantages |
---|---|
Hyatt Regency Hotel | Fast installation with one pass; less labor; less waste |
AISIN Texas Corporation Plant | Quick installation on a large scale; cost savings |
Cambridge Retrofit | 70% offsite fabrication; efficient onsite installation; high-quality results |
Tip: Prefabricated aluminum cladding systems can help keep projects on schedule, even in bad weather.
Labor and Equipment
Aluminum cladding systems need less labor than many traditional materials. Workers can handle the panels easily because they are light. This reduces the need for heavy lifting equipment. In many cases, a small team can install large areas quickly.
Compared to tilt-up concrete, which costs $80–$100 per square foot for labor and materials, aluminum cladding systems cost only $35–$55 per square foot. Over 40 years, maintenance costs are 62% lower than precast concrete and up to 70% lower than PVC. Certified aluminum cladding installations can also lower insurance premiums by 12–18%.
Aspect | Aluminum Cladding System | Alternative Materials / Notes |
---|---|---|
Installation cost | $35–$55/sq.ft. | Tilt-up: $80–$100/sq.ft. |
Labor needed | Low | Higher for concrete, stone, or multi-layer systems |
Maintenance cost (40yr) | 62% lower than precast concrete | Precast concrete and PVC have higher costs |
Handling | Lightweight, easy to move | Heavier materials need more equipment |
Aluminum cladding systems offer clear advantages in speed, labor, and cost. Builders can finish projects faster and save money on both installation and long-term upkeep.
Building Suitability
Commercial Use
Aluminum siding has become a top choice for commercial buildings in 2025. Many architects select aluminum siding for office towers, schools, hospitals, and shopping centers. This material meets strict safety codes, including the International Building Code (IBC) and NFPA 285 fire safety standards. These codes require cladding to protect people and property. Aluminum siding passes these tests, making it a reliable option for commercial projects.
Insulated metal panels, which include aluminum siding, deliver all four control layers—water, air, vapor, and thermal—in one product. This design creates a strong barrier against weather and temperature changes. Builders use aluminum siding in exterior applications because it resists rust, fading, and impact. The panels also help projects earn sustainability certifications. Many commercial buildings need fast construction. Aluminum siding installs quickly, saving time and labor costs.
Note: Aluminum siding offers high thermal performance, with R-values up to 7 per inch. This level of insulation reduces energy use and improves building performance.
A table below shows why commercial builders choose aluminum siding:
Feature | Benefit for Commercial Use |
---|---|
Code Compliance | Meets IBC, NFPA 285 |
Fast Installation | Reduces project timelines |
Durability | Withstands harsh environments |
Energy Efficiency | Lowers heating and cooling costs |
Residential Use
Homeowners and builders now use aluminum siding in many residential projects. Modern homes, apartments, and townhouses benefit from its durability and style. Aluminum siding protects homes from rain, snow, and wind. It does not rot or attract pests, so it lasts longer than wood or vinyl.
Studies show that homes with aluminum siding and rigid insulation lose less heat than traditional stick-built houses. Post-frame homes using metal panels and insulation can be up to 35% more energy efficient. This improvement means lower heating bills and better comfort for families. Aluminum siding also comes in many colors and finishes, so homeowners can match any design style.
Tip: Aluminum siding works well for both new homes and renovations. It adds value and reduces maintenance needs.
Aluminum siding supports strong building performance in residential settings. It meets safety codes and provides reliable protection for decades. Builders trust aluminum siding for its proven results in exterior applications.
Trends in 2025
Innovations in Aluminum Cladding
Aluminum cladding in 2025 shows many new features and improvements. Manufacturers use advanced extrusion and coating technologies to make panels stronger and more flexible. Digital fabrication and 3D modeling help designers create custom shapes and patterns. These tools also speed up installation and reduce mistakes on the job site.
Many companies now offer panels with special coatings. Some panels have anti-bacterial or anti-static surfaces. These features help keep buildings cleaner and safer. New insulation layers improve energy savings and make buildings more comfortable. Builders can choose from a wide range of colors and finishes, which gives architects more freedom to design unique facades.
Key trends in aluminum cladding innovation include:
- Use of lightweight, durable materials for easier handling and transport
- Improved insulation and thermal performance for energy-efficient buildings
- Digital tools for custom designs and faster installation
- Special coatings for health and safety, such as anti-bacterial finishes
- Focus on recyclable materials and sustainable production methods
Note: Green building certifications like LEED and BREEAM now drive demand for recyclable and energy-saving aluminum cladding panels.
Market and Code Changes
The aluminum cladding market continues to grow in 2025. Rapid urbanization and new infrastructure projects, especially in Asia-Pacific and the Middle East, increase demand for modern cladding solutions. The market size is expected to reach USD 18.8 billion by 2030, with a steady growth rate.
Building codes have become stricter. New rules focus on fire resistance, structural strength, and better insulation. These changes push manufacturers to develop safer and more efficient products. Environmental concerns also shape the market. Many governments support eco-friendly construction and encourage the use of recycled materials.
A summary of current market and code trends:
- Strong market growth due to urbanization and infrastructure development
- Stricter building codes for fire safety and energy efficiency
- Rising demand for sustainable and recyclable cladding materials
- Challenges from raw material price changes and supply chain issues
- Increased use of digital fabrication and 3D modeling in design and construction
Builders and architects must stay updated on these trends to choose the best cladding options for their projects in 2025.
Comparison with Other Cladding Materials
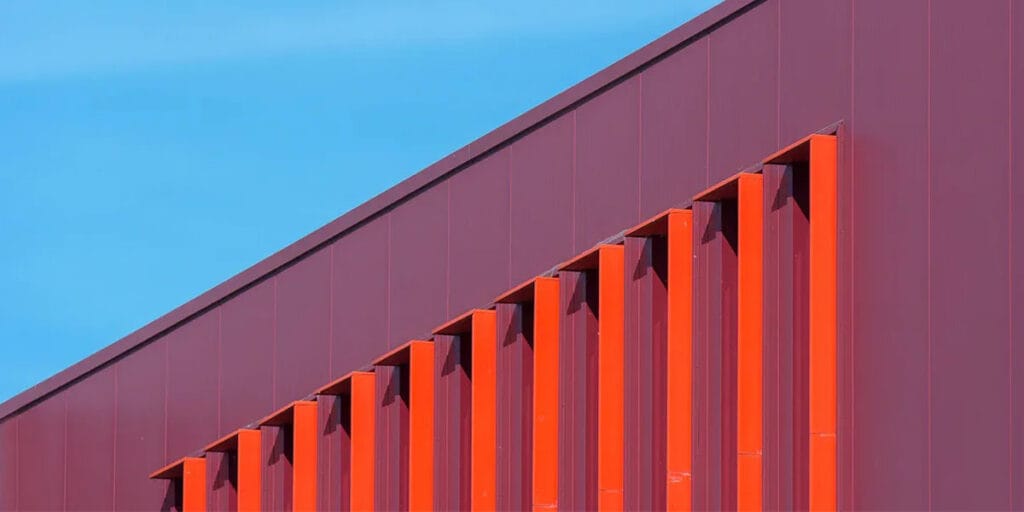
Key Takeaways
Builders and architects often look for the best material for their projects. The comparison with other cladding materials shows why many choose aluminum siding and solid aluminum cladding for modern buildings. Recent market research highlights several reasons for this trend. Aluminum siding and metal panels have become popular because they are lightweight, easy to install, and cost-effective. These features help reduce labor and transportation costs on job sites.
- Aluminum composite panels (ACPs) are light, which makes them easy to move and install.
- ACPs cost less than many other options, making them a smart choice for large projects.
- Aluminum siding and solid aluminum cladding resist corrosion, so they last longer in harsh weather.
- Metal panels, especially aluminum siding, need little maintenance. Owners can clean them easily, and they do not stain or attract mold.
- Fire-resistant versions of aluminum siding meet strict safety codes, which is important for tall buildings and public spaces.
- ACPs help keep buildings warm in winter and cool in summer. This energy efficiency lowers heating and cooling bills.
- The Asia Pacific region leads the market for aluminum siding and metal panels because of rapid city growth and strong government support for green building.
Note: The market for aluminum cladding panels is growing fast. Reports show the market will rise from $6.87 billion in 2024 to $9.09 billion by 2029. This growth comes from more cities, new buildings, and a push for energy-saving designs.
When looking at durability, solid aluminum cladding stands out. It does not rust, even in wet or salty air. Metal panels like aluminum siding last for decades with little care. In comparison with other cladding materials, wood can rot, vinyl can crack, and stone is heavy and hard to install. Metal cladding, especially solid aluminum cladding, offers a good balance of strength and weight.
The table below summarizes how aluminum siding and metal panels compare to other options:
Aspect | Key Takeaway |
---|---|
Market Dominance by Thickness | 4mm ACP panels hold 61.2% market share (2023), balancing affordability and performance. |
Coating Type | PVDF coatings have 34.5% revenue share; offer superior weather resistance, durability, and low maintenance costs. |
Fire Retardant Category | Fire retardant ACPs dominate with 68.5% market share due to strict fire safety regulations. |
End-Use Segment | Building & construction accounts for 55.3% market share; ACPs favored for aesthetics, insulation, and cost-effectiveness. |
Performance Benefits | ACPs provide lightweight, thermal insulation, acoustic properties, and aesthetic versatility. |
Environmental Impact | ACPs are recyclable, reduce energy use via insulation, and lower carbon footprint due to lightweight transport. |
Cost Benefit | 4mm panels are more affordable than thicker alternatives; PVDF coatings reduce long-term maintenance costs. |
Competition from Alternatives | Alternatives like FRP, HPL, stone, ceramic tiles, and glass offer advantages in impact resistance, fire safety, and sometimes cost, limiting ACP adoption in some markets. |
Market Drivers | Demand for sustainable, energy-efficient building materials boosts ACP adoption. |
Market Restraints | Availability of alternative materials with specific advantages and cost competitiveness may hinder ACP growth. |
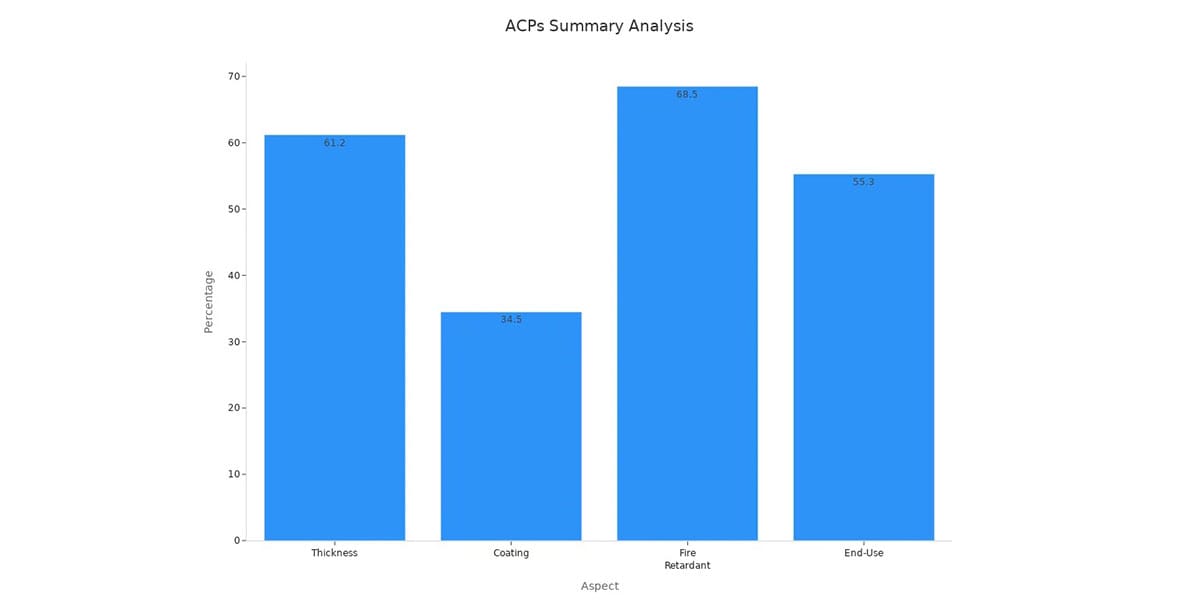
Solid aluminum cladding and aluminum siding also support green building goals. They are recyclable and help lower a building’s carbon footprint. Builders can use recycled aluminum, which saves energy and reduces waste. Metal panels, especially those with PVDF coatings, keep their color and finish for many years. This reduces the need for repainting or replacement.
Tip: Choosing solid aluminum cladding for facade usage can help projects meet strict energy and safety codes while keeping costs low.
However, the comparison with other cladding materials shows that some alternatives have their own strengths. Stone and ceramic tiles resist dents better. Glass and high-pressure laminates (HPL) offer unique looks. Some materials, like fiber-reinforced plastic (FRP), can cost less in certain markets. Still, aluminum siding and metal panels remain a top choice for many builders because they combine durability, safety, and design flexibility.
The aluminum market faces some challenges. Raw material prices can change quickly. Recycling helps, but not all scrap is high quality. New rules for cleaner production add costs, but they also make aluminum siding and solid aluminum cladding more sustainable.
Solid aluminum cladding stands out for its strength, light weight, and design flexibility. Builders often select solid aluminum cladding for projects that need fast installation and low maintenance. Solid aluminum cladding fits well in cavity wall assemblies, which help manage moisture and improve energy efficiency. When paired with mineral fiberglass or glass wool insulation, solid aluminum cladding can address fire safety concerns. Solid aluminum cladding offers a modern look and works for both commercial and residential buildings. Solid aluminum cladding resists rust and weather, making it a smart choice for harsh climates. Solid aluminum cladding also supports rainscreen systems, which protect buildings from water damage. Solid aluminum cladding provides a long lifespan and keeps its color over time. Solid aluminum cladding can lower long-term costs because it needs little upkeep. Solid aluminum cladding is easy to clean and does not attract pests. Solid aluminum cladding can help meet strict building codes. Solid aluminum cladding remains a top pick for builders who value durability, safety, and style. Solid aluminum cladding may not match stone for thermal performance in hot climates, but it excels in most other areas. Each project has unique needs, so readers should review their goals and consult a professional before choosing solid aluminum cladding.
FAQ
What makes aluminum wall panels a popular choice in 2025?
Aluminum wall panels offer strong durability, low maintenance, and modern style. Builders choose them for fast installation and energy efficiency. These panels also meet strict safety codes and support green building goals.
Can aluminum cladding panels be recycled?
Yes, aluminum cladding panels are fully recyclable. Many manufacturers use recycled aluminum to make new panels. Recycling aluminum saves energy and reduces waste, which helps protect the environment.
How do aluminum panels handle extreme weather?
Aluminum panels resist rust, fading, and water damage. They stay strong in rain, snow, and sun. Builders use them in coastal and humid areas because the panels do not corrode easily.
Are aluminum wall panels safe for tall buildings?
Yes. Aluminum wall panels meet fire safety standards like NFPA 285. Builders use them on high-rise buildings because they resist fire and help protect people and property.
What design options do aluminum panels offer?
Aluminum panels come in many colors, shapes, and finishes. Architects use them to create flat, curved, or patterned surfaces. These panels fit both modern and classic building styles.