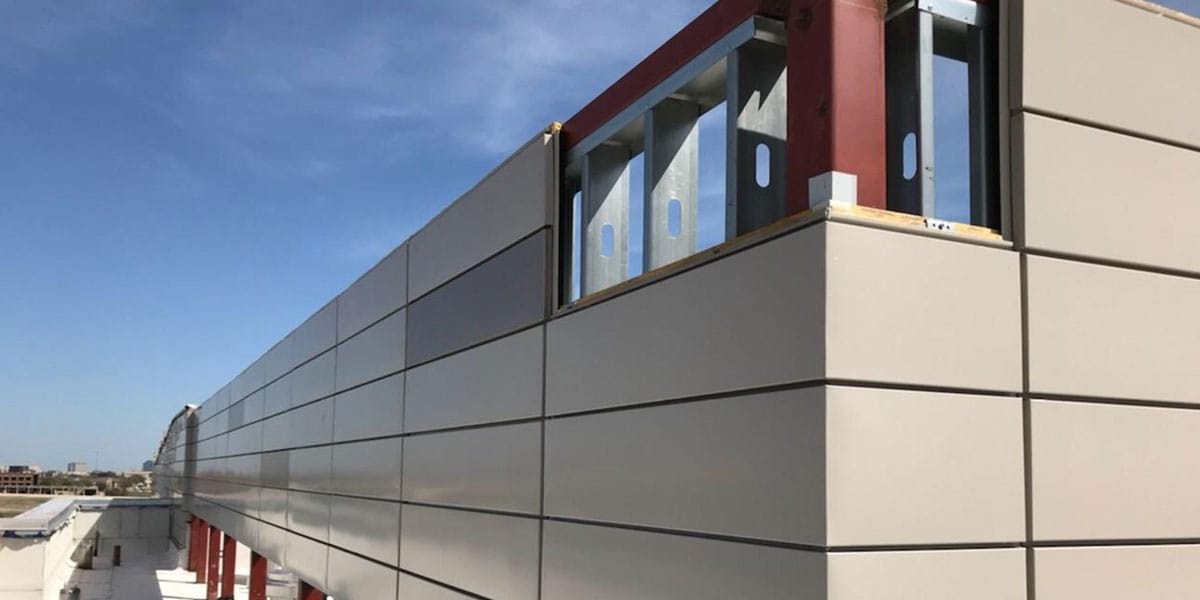
02 Jul Difference Between ACM and Aluminum Panels
Table of Contents
The difference between ACM and aluminum panels lies in their structure and performance. ACM panels use two thin aluminum sheets bonded to a polyethylene core. This design makes them lighter and stronger than solid aluminum panels. They resist weather, moisture, and UV rays, which helps prevent warping and fading. Many builders choose ACM for its flatness, easy installation, and wide range of finishes. Traditional aluminum panels do not have a core, making them heavier and less resistant to harsh weather. Understanding the difference between ACM and aluminum panels helps people select the right material for their project needs.
Key Takeaways
- ACM panels have two thin aluminum sheets bonded to a plastic core, making them lighter, stronger, and better insulated than solid aluminum panels.
- ACM panels resist weather, UV rays, and moisture well, keeping their flat shape and color longer, which makes them ideal for modern building designs and signage.
- Solid aluminum panels are heavier but easier to recycle and offer excellent durability, corrosion resistance, and fire safety for heavy-duty projects.
- ACM panels are easier to install and cost-effective for large projects, while aluminum panels suit applications needing full recyclability and structural strength.
- Choosing between ACM and aluminum panels depends on project needs like insulation, weight, finish options, maintenance, and environmental impact.
Quick Comparison
Features Table
Feature | ACM Panels | Aluminum Panels (Pure) |
---|---|---|
Composition | Aluminum sheets bonded to polyethylene core | Solid aluminum sheets |
Thickness | Varies, often similar thickness | |
Weight | Lightweight, strong, about half the weight | Heavier, depends on thickness |
Durability | Weather-resistant, rigid, UV and moisture safe | Durable, needs coating for corrosion resistance |
Recyclability | 100% recyclable, but complex due to composite | Easier to recycle as pure metal |
Energy Efficiency | Provides insulation, reduces heat transfer | Less insulating, higher thermal conductivity |
Cost-effectiveness | Cost-effective for cladding and signage | Often more expensive for cladding |
Surface Finish | Matte, gloss, brushed, mirror | Gloss, matte, brushed, mirror |
Print Compatibility | Optimized for UV & Latex printing | Suitable for digital and screen printing |
Fabrication Ease | Easy to cut, bend, and form | Easy to fabricate, but heavier |
Maintenance | Low, non-corrosive aluminum facers | Needs maintenance to prevent corrosion |
Signage, displays, framing, exterior/interior | Similar, often used in construction |
Tip: ACM panels offer a smooth, flat surface that works well for printing and modern designs.
Main Points
- ACM panels use two thin aluminum sheets with a plastic core. This makes them lightweight, strong, and easy to install.
- Aluminum panels are solid metal. They are heavier and may need extra coatings to prevent rust.
- ACM panels resist weather, UV rays, and moisture better than standard aluminum panels.
- High-quality ACM panels provide good insulation, soundproofing, and long-lasting color finishes.
- Aluminum panels are easier to recycle because they are pure metal. ACM panels are harder to recycle due to the plastic core.
- ACM panels often cost less for large projects like building cladding or signs.
- The Difference Between ACM and aluminum panels affects installation, durability, and maintenance needs.
- Builders choose ACM panels for their flatness, design flexibility, and easy handling. Aluminum panels work well where strength and full recyclability matter most.
What is ACM?
Structure
ACM stands for Aluminum Composite Material. Manufacturers create ACM panels by bonding two thin sheets of pre-painted aluminum to a solid core, usually made from polyethylene or other thermoplastic materials. This forms a three-layer sandwich panel. The aluminum layers provide strength and a modern look, while the core adds stability and insulation. Most ACM panels have a thickness of about 4 millimeters. The design ensures the panels stay flat and rigid, even when used in large sizes. Engineers include features like vapor management and concealed anchors to handle moisture and allow for expansion and contraction. Factories apply a protective film to the surface, which workers remove after installation to keep the finish clean and scratch-free.
Features
ACM panels offer several important features:
- Lightweight construction makes them easy to handle and install.
- The aluminum surface resists corrosion and harsh weather.
- The core provides thermal insulation and helps reduce noise.
- Panels come in many colors and finishes, including matte, gloss, and metallic.
- The structure keeps the panels flat and free from warps or buckles.
- ACM panels meet strict fire safety standards, such as ASTM E84 Class A or B ratings.
Note: The combination of durability, insulation, and design flexibility makes ACM panels a popular choice for modern buildings.
Uses
Builders and designers use ACM panels in many ways:
- Ventilated facades on buildings help control moisture and improve energy efficiency.
- Signage and wayfinding systems benefit from the smooth, customizable surface.
- Interior wall cladding adds color and durability to commercial and residential spaces.
- Column covers and canopies use ACM for weather resistance and style.
- Interior partitions and room dividers create modern, open spaces with privacy.
ACM panels adapt to many projects because they combine strength, light weight, and visual appeal.
What is an Aluminum Panel?
Structure
Aluminum panels are made from solid sheets of aluminum metal. Manufacturers often use alloys that include manganese or magnesium to improve strength and surface quality. The panels usually have a thickness of about 4 millimeters and can be cut to different sizes for various projects. During production, the aluminum sheets are pre-treated and coated with special paints. These coatings protect the panels from corrosion, dirt, and graffiti. The panels may also receive anodized or chemical conversion coatings to add color and extra protection. Most aluminum panels are lightweight and easy to handle. Installation methods include riveting, screwing, or suspending the panels on a substructure. Some builders use special adhesives, but mechanical fixing is more common for building facades.
Tip: Aluminum panels develop a natural oxide layer that helps protect them from rust and weather damage.
Features
Aluminum panels offer several important features that make them popular in construction and manufacturing:
- Lightweight design reduces the load on buildings and makes installation easier.
- High corrosion resistance comes from the natural oxide layer and protective coatings.
- Good thermal and electrical conductivity supports use in electrical and heat-related applications.
- Malleability allows the panels to be shaped and formed into many designs.
- Nonmagnetic properties make them suitable for sensitive electronic environments.
- Panels can have different finishes, such as bare aluminum, anodized, or painted surfaces.
Technical Characteristic | Description |
---|---|
Lightweight | Easy to handle and install, lowers structural load |
Corrosion-resistant | Natural oxide and coatings protect against weather and chemicals |
Good conductivity | Supports electrical and heat transfer uses |
Malleable and ductile | Allows shaping and custom designs |
Variety of finishes | Options include anodized, painted, or bare aluminum for different looks |
Uses
Aluminum panels serve many purposes in daily life and industry. In construction, they appear in window frames, curtain walls, roofing sheets, and facade panels. Builders use them for residential siding, gutters, and storefronts because of their weather resistance and strength. The transportation industry relies on aluminum panels for aircraft, trains, ships, and cars. These panels help reduce weight and improve fuel efficiency. In electrical systems, aluminum panels are used in power lines, transformers, and electronic devices due to their excellent conductivity. Many consumer goods, such as smartphones, laptops, and kitchen appliances, also use aluminum panels for their durability and modern appearance.
Aluminum panels combine strength, light weight, and corrosion resistance, making them a top choice for many applications in construction, transportation, and electronics.
Difference Between ACM
Flatness
ACM panels provide excellent flatness. The composite structure, with two thin aluminum sheets bonded to a plastic core, keeps the surface smooth and even. Solid aluminum panels can sometimes warp or bend, especially in large sizes. The Difference Between ACM and solid aluminum panels becomes clear when architects need a perfectly flat surface for cladding or signage. ACM panels stay flat over time, which helps maintain a clean and modern look.
Weight
Weight is a major Difference Between ACM and solid aluminum panels. ACM panels weigh about half as much as solid aluminum sheets. This lighter weight makes ACM panels easier to handle, transport, and install. Workers can lift and move ACM panels with less effort. The reduced weight also lowers the load on building structures. In contrast, solid aluminum panels are heavier and may require more support during installation.
Strength
Both ACM and aluminum panels offer good strength, but in different ways. ACM panels combine the strength of aluminum with the stability of a plastic core. This design resists bending and impact. Solid aluminum panels have natural metal strength, but they can dent or deform under heavy force. The Difference Between ACM and aluminum panels shows in how each material handles stress. ACM panels often perform better in applications where both strength and flexibility matter.
Insulation
ACM panels provide better insulation than solid aluminum panels. The plastic core in ACM panels helps block heat and cold, making buildings more energy efficient. Some ACM panels use special foam cores that improve thermal insulation and fire safety. These panels emit less heat during a fire and slow down the spread of flames. Solid aluminum panels do not insulate as well because metal transfers heat quickly. The Difference Between ACM and aluminum panels is important for projects that need to save energy or meet fire safety standards.
Durability
Durability is another key Difference Between ACM and aluminum panels. ACM panels go through many tests to check their strength and resistance to damage. Tests include measuring coating thickness, checking for scratches, and testing resistance to chemicals and impacts. ACM panels have coatings that protect against UV rays, moisture, and corrosion. They have proven to last in harsh climates, such as cold winters and hot summers. Solid aluminum panels also resist rust and weather, but they may need extra coatings for long-term protection.
Durability Test | ACM Panels Result |
---|---|
Coating Thickness | Uniform, protects against weather |
Scratch Resistance | High, resists surface damage |
Chemical Resistance | Strong, resists corrosion |
Impact Resistance | Withstands mechanical impacts |
Acid Resistance | Resists acid exposure |
Regular cleaning and proper care help both types of panels last longer.
Installation
ACM panels are easier to install than solid aluminum panels. The lighter weight allows workers to lift and position panels with less effort. Installers can cut, bend, and shape ACM panels using simple tools. The panels attach to buildings with screws, adhesives, or special clips. Solid aluminum panels are heavier and may require more people or equipment for installation. The Difference Between ACM and aluminum panels affects project speed and labor costs.
Finishes
ACM panels come in a wide range of finishes. Options include matte, gloss, metallic, and even custom colors. The surface stays smooth and bright for many years. Solid aluminum panels also offer different finishes, such as anodized or painted surfaces. However, ACM panels often provide more choices and better color consistency. The Difference Between ACM and aluminum panels can influence the final look of a building or sign.
Cost
Cost is a practical Difference Between ACM and aluminum panels. ACM panels usually cost less for large projects. The lighter weight reduces shipping and labor costs. The panels also need less maintenance over time. Solid aluminum panels can be more expensive, especially when thicker sheets are required. Builders often choose ACM panels for cost-effective cladding and signage.
Environmental Impact
Environmental impact matters when choosing building materials. ACM panels are recyclable, but the process is more complex because of the plastic core. Solid aluminum panels are easier to recycle since they are pure metal. However, ACM panels use less aluminum overall, which saves resources. The Difference Between ACM and aluminum panels affects recycling and sustainability goals. Builders should consider both the ease of recycling and the amount of material used.
Pros and Cons
ACM Panels
ACM panels offer many advantages for builders and designers. These panels stay flat and smooth after installation. The bonded core keeps the surface from wrinkling, which prevents oil canning. This feature helps maintain a modern and clean look for many years. ACM panels weigh less than solid aluminum panels, so workers can install them faster and with less effort. The panels also provide good thermal insulation, which can lower heating and cooling costs. Many people choose ACM panels because they come in a wide range of finishes, including metallic, matte, wood, and stone designs. Maintenance needs stay low, and the panels resist weather, UV rays, and moisture.
However, ACM panels have some drawbacks. The plastic core can make recycling more difficult compared to pure aluminum. While ACM panels last 40–50 years with proper care, their lifespan may be shorter than some solid aluminum panels. Some projects may require panels with higher fire resistance or easier recyclability.
Tip: ACM panels avoid oil canning, so they keep a flat and attractive appearance over time.
Feature | ACM Panels (Pros) | ACM Panels (Cons) |
---|---|---|
Flatness | Maintains flat surface, no oil canning | – |
Weight | Lightweight, easy to install | – |
Insulation | Good thermal insulation | – |
Cost | Budget-friendly | – |
Maintenance | Low maintenance | – |
Recyclability | Recyclable, but core complicates process | Harder to recycle than pure aluminum |
Lifespan | 40–50 years with care | May be shorter than solid aluminum |
Aluminum Panels
Aluminum panels also provide many benefits. These panels resist insects, fire, and water. They do not rust or absorb moisture, so they work well in humid or hot climates. Aluminum panels last a long time—some can last up to 80 years if maintained well. The panels are easy to recycle, and many manufacturers use recycled aluminum to make new panels. Aluminum panels come in many styles and colors, and builders can paint or anodize them for different looks. The panels are also cost-effective compared to other siding systems.
There are some disadvantages. Aluminum panels can dent or scratch easily. Repairs may require professional help, and matching the color can be hard. Traditional aluminum panels do not insulate well, so extra insulation may be needed. The metal surface can make buildings look industrial, which may not fit every design. Flat sheet aluminum panels are prone to oil canning, which can affect the appearance over time. The Difference Between ACM and aluminum panels often comes down to these practical and visual factors.
Pros of Aluminum Panels | Cons of Aluminum Panels |
---|---|
Insect-proof, fire-resistant | Susceptible to dents and scratches |
Extremely durable, recyclable | Poor sound insulation (traditional panels) |
Waterproof, rustproof | Industrial appearance, oil canning possible |
Variety of styles and colors | May need extra insulation |
Cost-effective, low maintenance | Repairs can be difficult |
Choosing Panels
Project Needs
Selecting the right panel depends on the specific needs of each project. Builders and designers must consider several important criteria before making a decision. The following table compares key factors for aluminum panels and ACM panels:
Criteria | Aluminum Panels | ACM Panels |
---|---|---|
Material Structure | Solid, non-laminated aluminum | Two thin aluminum sheets bonded to a non-aluminum core |
Application Type | Heavy-duty, structural, aerospace, military, facades | Exterior and interior cladding, modern architectural designs |
Weight & Installation | Lightweight, ease of installation, lower labor costs | Generally lighter, easier to install due to laminated structure |
Finishes & Colors | Most finishes available | Wider range, including high-gloss, stainless steel, wood effects |
Fabrication Procedures | Bending, cutting, welding; more difficult but precise | More flexible fabrication, modern machines improve accuracy |
Fire Safety | Non-combustible, meets regulations | Improving fireproof characteristics, some regulatory approvals |
Impact Resistance | Rigid and durable | High impact strength |
Corrosion Resistance | Good | Superior corrosion resistance |
Sound Insulation | N/A | Better sound insulation |
Weather & UV Resistance | Good | More weather-resistant, less maintenance |
Cost & Maintenance | Cost-effective, lower upkeep | Generally more weather-resistant, less maintenance |
Project managers should review these criteria to match the panel type to the building’s requirements. For example, a project that needs high impact resistance and modern finishes may benefit from ACM panels. Projects that require non-combustible materials or heavy-duty structural support may favor solid aluminum panels.
Tip: Always check local building codes and fire safety standards before choosing a panel type.
ACM panels and aluminum panels have different structures, strengths, and uses. Each material works best for certain projects. Builders should review the pros and cons before making a choice. They need to match the panel type to the project’s needs.
ACM panels offer flatness and easy installation.
Aluminum panels provide durability and easy recycling.
For complex projects, experts can help select the right material.
FAQ
What makes ACM panels different from solid aluminum panels?
ACM panels have two thin aluminum sheets with a plastic core. Solid aluminum panels use only metal. This structure gives ACM panels better flatness, lighter weight, and more insulation.
Can ACM panels be recycled?
ACM panels can be recycled, but the process is more complex because of the plastic core. Recycling centers must separate the aluminum from the core before reusing the materials.
Are ACM panels safe for outdoor use?
ACM panels resist weather, UV rays, and moisture. Builders use them for building exteriors, signs, and facades. The panels keep their color and shape in harsh climates.
Which panel is better for sound insulation?
Panel Type | Sound Insulation |
---|---|
ACM Panel | Good |
Aluminum Panel | Poor |
ACM panels provide better sound insulation because of the plastic core. Solid aluminum panels do not block sound as well.