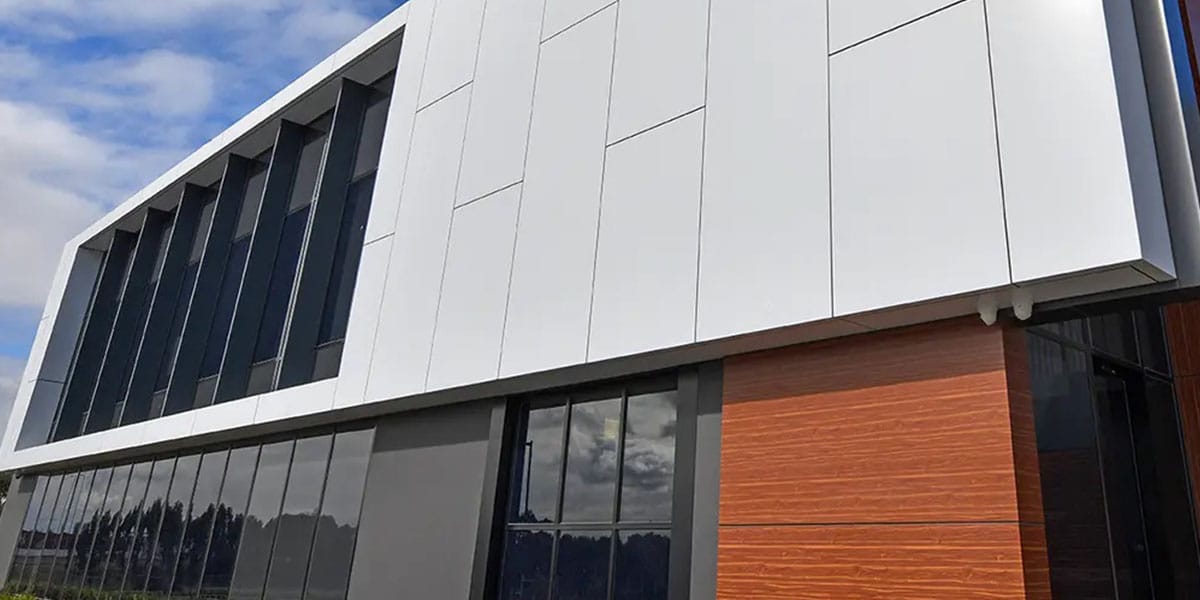
25 Mar Comparing PVDF Aluminum Composite Panels to Other Types
Table of Contents
- 1 Material Composition and Coating
- 2 Cost Comparison
- 3 Durability and Performance
- 4 Aesthetic Appeal
- 5 Construction and Installation Processes
- 6 Environmental and Residual Value Considerations
PVDF aluminium composite panels stand out in the construction industry due to their exceptional properties. These panels resist corrosion, withstand UV exposure, and maintain their appearance over time. Their popularity continues to grow, with the global market valued at $2.5 billion in 2023 and projected to reach $4.3 billion by 2032. Urbanization and the demand for sustainable infrastructure drive this growth. You can find PVDF aluminium composite panels in both exterior and interior applications, where durability and aesthetic appeal are essential.
Material Composition and Coating
PVDF Aluminum Composite Panels
Core materials and PVDF coating properties
The core of a PVDF aluminum composite panel typically consists of a lightweight, non-combustible material, such as mineral-filled cores or polyethylene. This core is sandwiched between two aluminum sheets, creating a durable yet lightweight structure. The outer surface features a PVDF coating, which is a blend of 70% PVDF and 30% resin. This composition ensures high weather resistance, chemical resistance, and protection against fading or chalking. The PVDF coating also meets AAMA 2605 standards, making it suitable for high-performance building exteriors.
Advantages of PVDF coating in weather resistance and chemical resistance
The PVDF coating offers several advantages:
- Weather Resistance: It withstands UV rays, temperature fluctuations, and harsh environmental conditions.
- Chemical Resistance: The nonreactive thermoplastic fluoropolymer resists corrosion and pollutants.
- Durability: It retains color and gloss over time, ensuring a long-lasting aesthetic appeal.
These properties make PVDF aluminum composite panels ideal for both exterior and interior applications where durability and environmental resistance are critical.
Other Composite Panel Types
PE Aluminum Composite Panels
PE aluminum composite panels use a polyethylene core and a polyester coating. While they are cost-effective, they lack the durability and weather resistance of PVDF panels. These panels are better suited for indoor applications or areas with less demanding environmental conditions.
HPL Panels
High-Pressure Laminate (HPL) panels consist of resin-impregnated kraft paper layers bonded under high pressure. They offer decent durability but are prone to fading and require more maintenance compared to PVDF panels.
Fiber Cement Panels
Fiber cement panels combine cement, sand, and cellulose fibers. They are heavy and durable but lack the flexibility and smooth finish of PVDF aluminum composite panels. Their porous surface also makes them more susceptible to staining.
Key Differences in Material Composition
Durability and resistance to environmental factors
PVDF aluminum composite panels outperform other types in durability and environmental resistance. Unlike PE panels, which are suitable for mild conditions, PVDF panels resist UV rays, corrosion, and temperature changes. Fiber cement panels are durable but heavy and less versatile. HPL panels, while sturdy, fade faster under prolonged exposure to sunlight.
Maintenance requirements
You will find PVDF aluminum composite panels easier to maintain. Their PVDF coating resists scratches, chemicals, and pollutants, reducing cleaning and repair needs. In contrast, HPL and fiber cement panels require more frequent upkeep due to their susceptibility to stains and fading.
Cost Comparison
PVDF Aluminum Composite Panels
Initial cost and long-term value
When considering PVDF aluminum composite panels, you should evaluate both their upfront cost and their long-term benefits. These panels typically cost between $7 and $12 per square foot. While this may seem higher than other options, their durability and low maintenance requirements make them a cost-effective choice over time. The PVDF coating ensures resistance to weathering, fading, and chemical damage, reducing the need for frequent repairs or replacements. This longevity translates into significant savings, especially for large-scale projects.
Other Composite Panel Types
Cost of PE aluminum composite panels
PE aluminum composite panels are among the most affordable options. Their price reflects their simpler composition and lower durability. These panels are ideal for indoor applications or areas with minimal environmental stress. However, their limited lifespan and higher maintenance needs can increase costs in the long run.
Cost of HPL and fiber cement panels
HPL panels fall in the mid-range cost category. They offer decent durability but require regular upkeep, which adds to their overall expense. Fiber cement panels, on the other hand, are heavier and more expensive to install. Their porous surface also demands frequent cleaning, further increasing maintenance costs.
Factors Influencing Cost
Material quality and coating
The type of core material and surface coating significantly impacts the cost of composite panels. For example, fire-resistant cores and PVDF coatings are more expensive but provide superior performance. The table below highlights these factors:
Factor | Description | Impact on Cost |
---|---|---|
Core Material | PE cores are cheaper, while fire-resistant cores cost more. | Fire-resistant cores increase durability and safety. |
Surface Coating | PVDF coatings offer better weather resistance. | Higher-quality coatings raise the price. |
Installation and maintenance costs
Installation complexity also affects the total cost. PVDF aluminum composite panels are lightweight, making them easier and less expensive to install. In contrast, fiber cement panels require specialized equipment due to their weight. Maintenance costs vary as well. PVDF panels need minimal upkeep, while HPL and fiber cement panels demand more frequent attention.
Durability and Performance
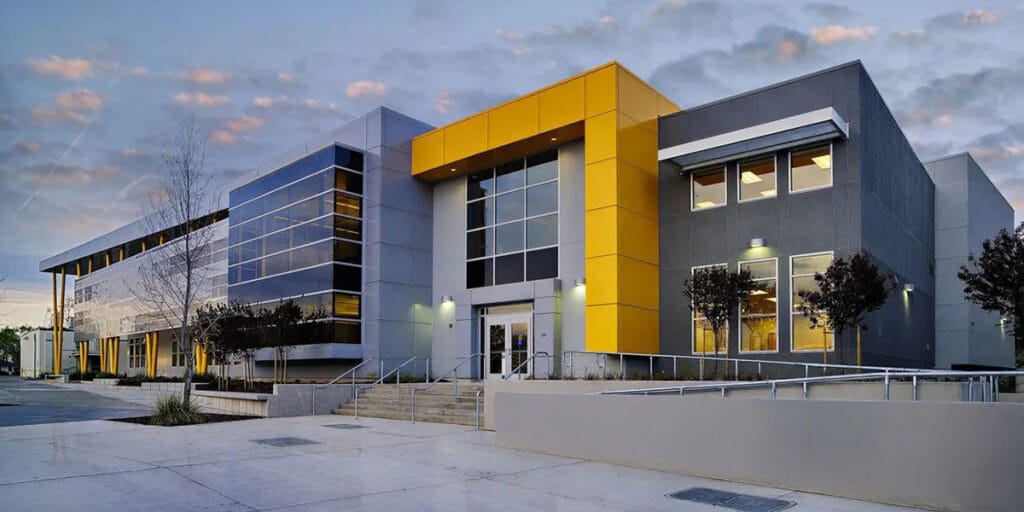
Weather Resistance
PVDF panels in extreme climates
You can rely on PVDF aluminum composite panels to perform exceptionally well in extreme weather conditions. Their specialized coating enhances durability, offering excellent UV resistance and superior color retention. Even after prolonged exposure to harsh environments, these panels maintain their flatness and aesthetic appeal. This makes them a reliable choice for both interior and exterior applications, ensuring they withstand the elements effectively.
Comparison with other panel types
When compared to other panel types, PVDF panels stand out due to their resilience. PE aluminum composite panels lack the same level of UV resistance and tend to degrade faster under intense sunlight. Fiber cement panels, while durable, are prone to staining and may not retain their appearance as well. HPL panels, on the other hand, fade more quickly when exposed to prolonged sunlight, requiring frequent maintenance.
Fire Resistance
Fire-retardant properties of PVDF panels
Modern PVDF aluminum composite panels often feature fire-retardant cores, making them a safer option for construction. These cores include mineral substances or honeycomb structures that comply with international fire safety regulations. You will find these panels suitable for high-rise buildings, airports, and hospitals due to their enhanced safety features.
Fire performance of PE, HPL, and fiber cement panels
- Early PE aluminum composite panels spread fire quickly, posing significant risks.
- Fire-rated ACPs with mineral-filled cores offer better fire resistance and meet local building codes.
- Fiber cement panels provide good fire resistance but lack the flexibility and lightweight nature of PVDF panels.
Mechanical Properties
Impact resistance and flexibility
PVDF aluminum composite panels combine lightweight construction with superior impact resistance. Their structural stability ensures they can handle mechanical stress without compromising performance. This makes them ideal for projects requiring both durability and flexibility.
Longevity under mechanical stress
These panels maintain their integrity even under prolonged mechanical stress. Their durability and resistance to harsh weather conditions make them a long-lasting solution for various applications. The table below highlights their key mechanical properties:
Property | Description |
---|---|
Impact Resistance | Superior impact resistance |
Aesthetic Appeal
Design Versatility
Color and finish options for PVDF panels
When it comes to design versatility, PVDF aluminum composite panels offer a wide range of color and finish options. These panels allow you to achieve the exact look you desire for your project. The following table highlights the available choices:
Color Options | Finish Types |
---|---|
Solid | Glossy |
Metallic | Mirror |
Marble | Brush |
Wooden | |
More than 60 Solid colors | |
More than 60 Metallic colors | |
Customized colors: PANTONE and RAL |
These options make PVDF panels suitable for both modern and traditional designs. Whether you want a sleek metallic finish or a natural wooden appearance, these panels can meet your aesthetic needs.
Aesthetic limitations of other panel types
Other panel types, such as HPL and fiber cement panels, lack the same level of design flexibility. HPL panels offer fewer color and finish options, while fiber cement panels often come in limited shades and textures. This restricts their use in projects requiring unique or vibrant designs.
Surface Quality
Smoothness and uniformity in PVDF panels
PVDF aluminum composite panels stand out for their exceptional surface quality. Their smooth and uniform finish enhances the overall appearance of any structure.
- These panels maintain excellent flatness, ensuring a polished look.
- The PVDF coating resists scratches, chemicals, and pollutants, keeping the surface low-maintenance and visually appealing.
Surface texture in HPL and fiber cement panels
In contrast, HPL and fiber cement panels often have a rougher texture. Fiber cement panels, in particular, feature a porous surface that can stain easily. This makes them less suitable for projects where a flawless finish is essential.
Customization Options
Printing and patterning on PVDF panels
PVDF aluminum composite panels excel in customization. You can digitally print high-quality designs on both sides of these panels. The table below outlines their customization capabilities:
Customization Type | Details |
---|---|
Printing | Can be digitally printed on both sides with high print quality. |
Finishes | Available in solid, metallic, marble, wooden, brush, glossy, and mirror finishes. |
Durability | Weather resistant, fire resistant, and environmentally friendly. |
Customization capabilities of other panels
Other panel types, such as HPL and fiber cement panels, offer limited customization. While HPL panels can include some patterns, they lack the advanced printing and finish options available with PVDF panels. Fiber cement panels are even more restricted, often limited to basic colors and textures.
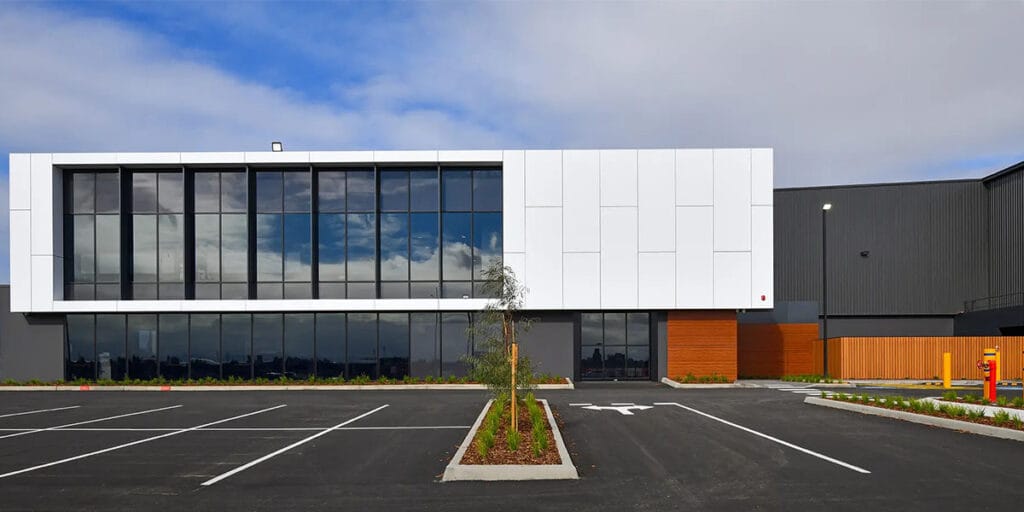
Construction and Installation Processes
Ease of Installation
Lightweight nature of PVDF panels
PVDF aluminum composite panels are lightweight, making them easier to handle during installation. Their reduced weight minimizes strain on construction workers and speeds up the process. You can also transport these panels more efficiently, which reduces logistical challenges. The lightweight design ensures compatibility with a variety of structural systems, enhancing their versatility in construction projects.
Installation challenges with other panel types
Other panel types, such as fiber cement panels, present more challenges during installation. Their heavy weight requires specialized equipment and additional labor, increasing both time and costs. HPL panels, while lighter than fiber cement, often need precise alignment and careful handling to avoid damage. PE aluminum composite panels are easier to install but lack the durability and performance of PVDF panels, making them less suitable for demanding applications.
Compatibility with Building Systems
PVDF panels in modern construction
PVDF aluminum composite panels integrate seamlessly with modern construction systems. Their versatility allows you to use them in various applications, including:
- Building facades and cladding.
- Interior design and decorative elements.
- Signage and branding.
- Innovative designs with LED lighting and smart technologies.
These panels also offer aesthetic flexibility with a wide range of colors and finishes. Their lightweight design enhances structural stability, making them ideal for complex architectural projects.
Limitations of other panels in complex designs
Other panel types often struggle to meet the demands of modern construction. Fiber cement panels, for instance, lack the flexibility needed for intricate designs. HPL panels provide some design options but fall short in integrating advanced technologies like LED systems. PE aluminum composite panels, while versatile, do not offer the same level of durability or aesthetic appeal as PVDF panels.
Maintenance and Repairs
Cleaning and upkeep of PVDF panels
PVDF aluminum composite panels require minimal maintenance. Their smooth surface resists dirt, stains, and pollutants, making cleaning quick and easy. You can simply use water and mild detergent to restore their appearance. The PVDF coating also protects against scratches and fading, reducing the need for frequent repairs.
Maintenance needs of other panel types
Other panel types demand more upkeep. Fiber cement panels, with their porous surface, are prone to staining and require regular cleaning. HPL panels fade faster under sunlight, necessitating periodic refinishing. PE aluminum composite panels, while easier to clean, lack the long-term durability of PVDF panels, leading to higher maintenance costs over time.
Environmental and Residual Value Considerations
Sustainability
Recyclability of PVDF panels
PVDF aluminum composite panels offer significant sustainability benefits due to their recyclability. These panels are made from recycled aluminum and can be fully recycled at the end of their lifecycle. This reduces waste and supports eco-friendly practices in construction. Additionally, their production process aligns with global goals to minimize resource consumption and promote environmental responsibility.
Benefit | Description |
---|---|
Recyclability | Panels are made from recycled aluminum and are fully recyclable at end-of-life. |
Eco-friendly Practices | Supports eco-friendly practices and reduces waste. |
Long-term Sustainability | Ensures sustainability over the lifecycle of the product. |
By choosing PVDF panels, you contribute to a greener future while ensuring long-term sustainability in your projects.
Environmental impact of other panel types
Other panel types, such as PE aluminum, HPL, and fiber cement panels, have varying environmental impacts. PE aluminum panels often raise concerns due to their lower recyclability and higher carbon footprint. Aluminum production contributes to about 2% of global CO2 emissions, though newer products now feature recyclable cores and low-emission coatings. Fiber cement panels, which make up 30% of exterior cladding in North America, are less recyclable and require more energy-intensive production processes. These factors make PVDF panels a more sustainable choice for environmentally conscious projects.
Residual Value
Long-term value retention of PVDF panels
PVDF aluminum composite panels retain their value over time due to their durability and low maintenance requirements. Their resistance to weathering, fading, and chemical damage ensures they remain visually appealing and structurally sound for years. This longevity makes them a cost-effective investment, especially for large-scale projects. You can expect these panels to maintain their performance and appearance, even in demanding environments.
Comparison with other panels in resale or reuse
When compared to other panel types, PVDF panels offer superior resale and reuse potential. Their recyclability and durability make them attractive for secondary markets. In contrast, PE aluminum panels degrade faster, reducing their resale value. Fiber cement panels, while durable, are heavier and harder to repurpose. HPL panels, with their limited lifespan, also fall short in retaining value. PVDF panels stand out as a reliable and sustainable option for long-term use.
PVDF aluminum composite panels combine durability, weather resistance, and aesthetic versatility, making them a top choice for many applications. You benefit from their ability to withstand harsh conditions while maintaining their structural integrity and vibrant appearance.
- The PVDF coating resists corrosion, erosion, and extreme weather.
- Panels retain their color and luster over time.
- A wide range of colors and textures supports diverse design needs.
Other panel types may suit specific budgets or fire safety requirements. Always evaluate your project’s cost, durability, and environmental goals to select the best option.